CNC machining has revolutionized the manufacturing industry by offering numerous advantages over traditional manufacturing methods. This advanced technology uses computer control to produce consistently precise and accurate results with various materials. As a result, manufacturers and machinists across various industries rely on this versatile and cost-effective process to create intricate designs with minimal wasted material.
Precision and Accuracy
CNC machining is highly regarded for its precision and accuracy. This manufacturing process involves computer-controlled machines that execute tasks with remarkable consistency and repeatability. CNC machining delivers high precision parts with tight tolerances, ensuring greater accuracy compared to manual machining.
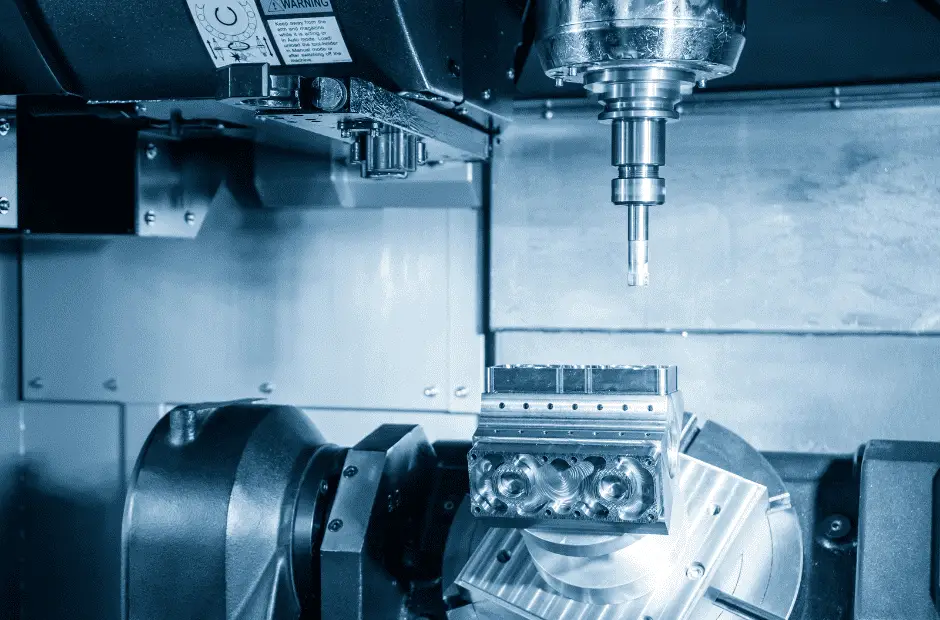
In the world of manufacturing, precision and accuracy are essential for producing high-quality components. Thanks to the use of computer programming, CNC machines can produce parts with incredibly tight tolerances, maintaining dimensions within fractions of a millimeter. Such precision results in fewer errors, reduced material waste, and higher degrees of conformity among produced parts.
Greater accuracy in CNC machining is achieved through the elimination of human error. Since the machines follow programmed instructions, the likelihood of mistakes is significantly diminished. This level of accuracy not only improves the quality of the finished products but also reduces production time, as there is minimal need for reworking or scrapping defective parts.
Overall, the precision and accuracy offered by CNC machining make it an ideal choice for industries that require consistency and exactitude in their manufactured components. With the ability to deliver high precision parts with tight tolerances, CNC machining ensures superior quality and reliable outcomes in the production process.
Efficiency and Speed
CNC machining is well-known for its efficiency and speed in the manufacturing industry. The use of computer-controlled machines allows for a significant increase in production speed when compared to traditional manufacturing methods. CNC machines eliminate the need for manual intervention during production, increasing the accuracy of the process while reducing potential errors and waste.
These machines can operate at high speeds, further enhancing their efficiency. CNC tools can be precisely programmed to perform complex tasks with remarkable accuracy, making them ideal for a range of applications, from small-scale prototyping to mass production of intricate components. The automated nature of CNC machining results in fewer delays and interruptions, allowing for consistent production speed and an overall increase in operational efficiency.
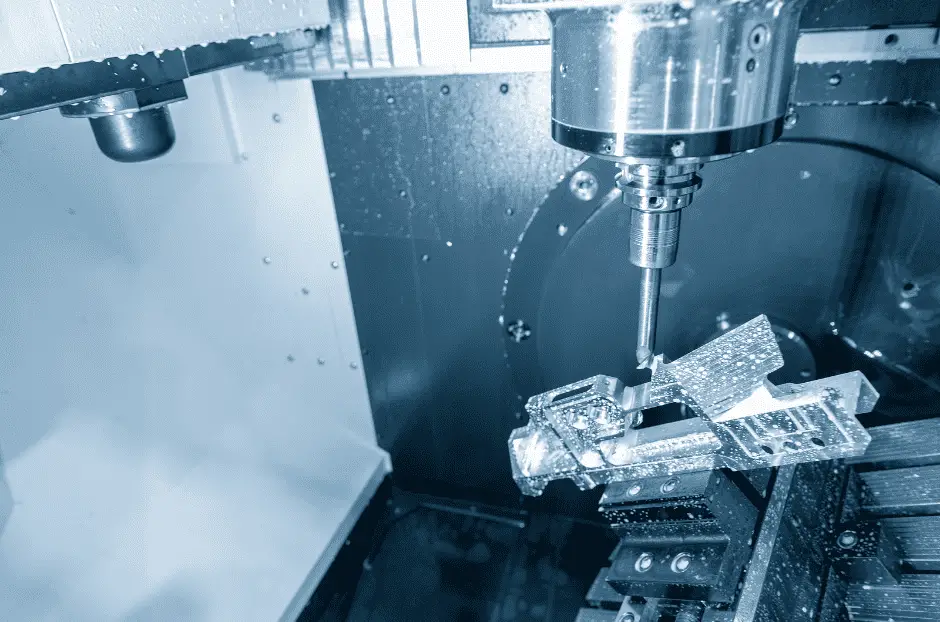
Not only do CNC machines contribute to increased production speed and efficiency, but they also enable manufacturers to produce a wider range of components and materials. By utilizing multiple tools in a single setup, CNC machines can effectively reduce setup times, allowing for faster production rates without sacrificing quality or accuracy.
In terms of energy consumption, CNC machines are typically more energy-efficient than conventional manufacturing tools. This is because CNC machines can be programmed to operate at optimal conditions, minimizing any energy wastage during the manufacturing process. This efficiency translates to lower operating costs, benefitting both manufacturers and consumers alike.
To summarize, the advantages of CNC machining in terms of efficiency and speed include:
- Increased production speed due to computer-controlled processes
- Enhanced precision and reduction of errors, resulting in less waste
- Faster setup times and the ability to produce a wide range of components
- Improved energy efficiency, leading to lower operational costs
Overall, the efficiency and speed offered by CNC machines make them an indispensable asset for modern manufacturing processes.
Cost Reduction
CNC machining is a cost-effective method for producing various components and provides several ways to reduce production costs. One of the primary benefits of using CNC machines is the ability to cut costs related to labor and materials. The automated nature of CNC machines significantly decreases labor costs, as fewer operators are required to oversee production processes.
Moreover, precise control over machining allows manufacturers to produce components with minimal material waste, thereby reducing material costs. The ability to consistently create intricate parts with tight tolerances also decreases post-production finishing requirements, which can add to overall expenses.
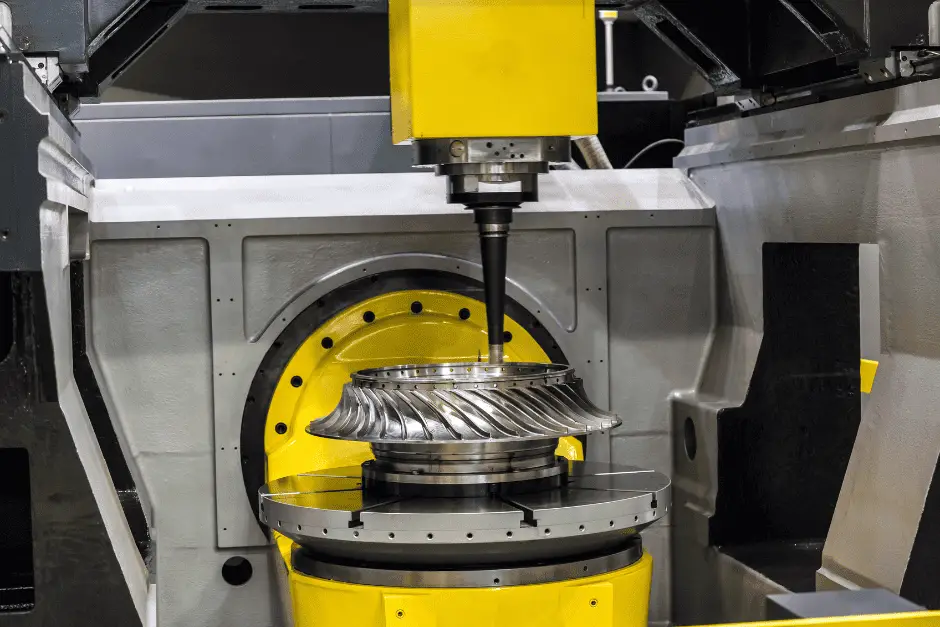
Another advantage of CNC machining is the reduction in maintenance costs. The advanced technology employed in CNC machines allows for self-diagnostics and built-in error prevention, minimizing downtime and lowering maintenance expenditures. Additionally, CNC machines are known for their reliability and consistent performance, further alleviating the need for frequent repairs.
Regarding energy consumption, CNC machining has improved over time, making it a more efficient and environmentally friendly manufacturing process. This efficiency translates to lower electricity consumption and subsequently reduced utility costs for manufacturers.
In summary, advantages of CNC machining in cost reduction include:
- Lower labor costs due to automation
- Reduced material waste, resulting in lower material costs
- Minimal post-production finishing requirements
- Decreased maintenance costs and improved reliability
- Lower energy consumption and related expenditures
CNC machining offers affordable solutions for manufacturers, making it an ideal choice for those looking to cut costs without compromising on quality and precision.
Reduced Human Error
CNC machining, also known as computer numerical control machining, significantly reduces human error in the manufacturing process. Automation plays a key role in the precision and accuracy of this technology. Unlike traditional manual labor methods, CNC machines rely on digital templates and computer-aided control to execute intricate cutting and shaping tasks.
The shift from manual labor to automation not only minimizes the chances of errors but also enhances productivity and cost-effectiveness across various industries. As a result, CNC machines have become the preferred choice for many manufacturers, particularly those in the medical equipment, automobile, and aerospace sectors.
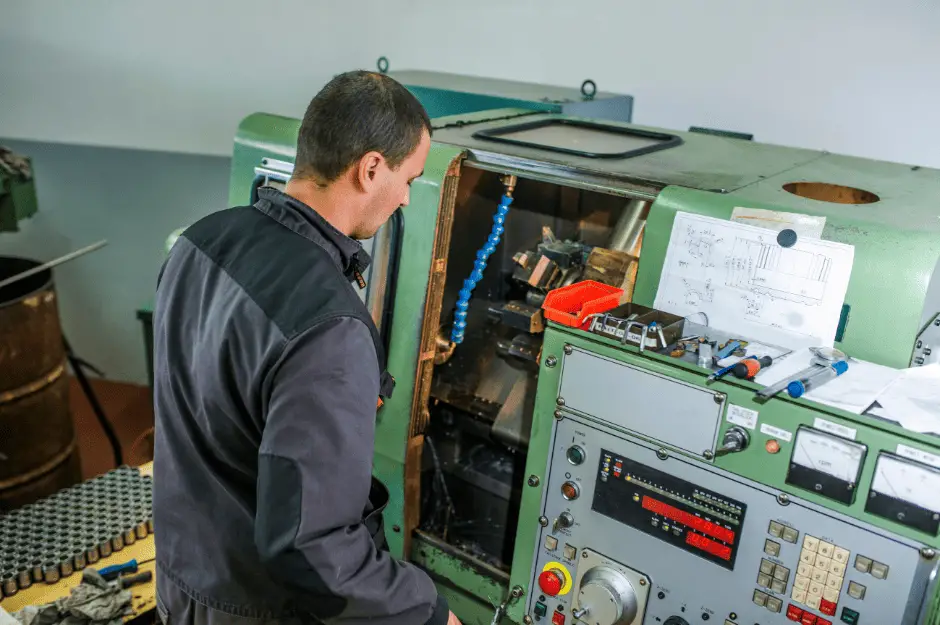
By utilizing a software-driven process, CNC machining ensures consistent and high-quality output. Its ability to repetitively execute specific actions without deviations led to the minimization of waste materials and defects related to human intervention. Consequently, CNC machining has emerged as a powerful tool for maintaining quality control and lowering production costs by reducing the need for additional personnel.
In summary, the advantages of CNC machining in reducing human error stem from its reliance on automation, computer numerical control, and the reduction of manual labor. This innovative technology enables industries to produce precise components with greater efficiency and accuracy, leading to overall improved manufacturing processes.
Versatility and Flexibility
CNC machining offers a high level of versatility and flexibility in the manufacturing process. It can work with a wide range of materials, including metals, plastics, and composites, making it suitable for various industries. The flexibility of CNC machining allows for intricate designs and geometry, enabling the production of parts with complex shapes and features.
One of the key benefits of CNC machining is its ability to perform various operations such as milling, turning, and drilling. This enables manufacturers to create prototypes and final products with precise accuracy and consistency. Furthermore, CNC machines can easily adapt to different production requirements, making them suitable for both small-scale and large-scale manufacturing processes.
Incorporating CNC machining into the production process offers numerous advantages in terms of design capabilities. The use of computer-aided design (CAD) software allows for the creation of intricate and detailed designs with minimal material waste. Additionally, CNC machining provides the flexibility to easily reshape and redesign existing parts without having to start from scratch.
Overall, the versatility and flexibility of CNC machining make it a valuable asset in modern manufacturing. Its ability to work with various materials, create complex shapes, and adapt to different production needs makes CNC machining a popular choice for industries looking to produce high-quality, diverse products.
Safety and Reliability
CNC machining offers many advantages in terms of both safety and reliability compared to traditional manufacturing methods. One key factor that improves safety is the reduction of direct human interaction with the machinery during operation. The automated nature of CNC machines not only reduces the risk of injury but also enables operators to focus on other aspects of production, such as quality control and documentation.
In terms of construction, CNC machines are built with high-quality materials, making them more durable and precise. This reliability is further enhanced by the use of advanced software programs, which undergo iterative optimization to develop the most efficient and accurate ways to produce components, leading to minimal waste. The precision and efficiency of CNC machines minimize the likelihood of producing faulty parts that need to be discarded, making the entire production process more resource-effective and cost-efficient.
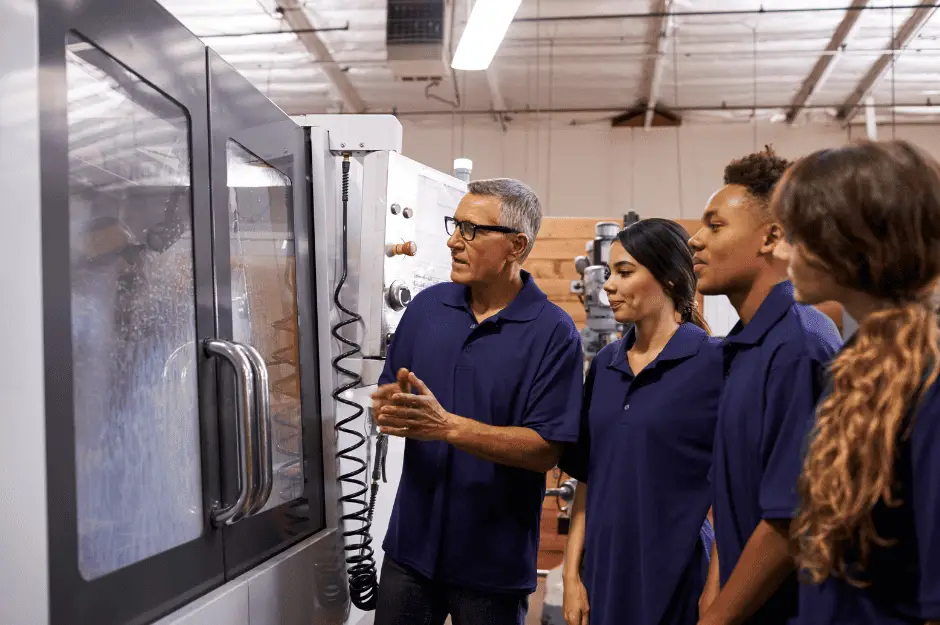
When it comes to assembly, CNC machining allows for quicker and more accurate production of parts. This not only streamlines the entire manufacturing process but also reduces the possibility of errors that could lead to safety issues in the final product. Furthermore, CNC machines can be easily integrated with other automated manufacturing systems, creating seamless production lines that help industries stay competitive in terms of both assembly speed and quality.
To ensure a safe workplace, some essential safety tips for CNC machinists include keeping the doors closed during operation, maintaining and cleaning machinery regularly, and providing proper operator training. These measures help to prevent accidents and maintain the reliability of CNC machines.
CNC machining’s advantages, which include safety, precision, and speed in construction and assembly, make it the preferred manufacturing method for various industries such as medical equipment, automobile, and aerospace. With continuous technological advancements and proper adherence to safety guidelines, CNC machining is poised to remain a crucial player in modern manufacturing.
Industries and Applications
CNC machining offers numerous advantages across various industries. It is a reliable and efficient process for producing complex components, thanks to its high precision and repeatability. This section will discuss the industries and applications of CNC machining.
The aerospace industry heavily relies on CNC machining due to the need for lightweight and high-strength components. CNC machines can process a wide range of materials that are suitable for aerospace applications, such as aluminum, titanium, and engineered plastics. Efficient production of intricate parts with tight tolerances is essential in aerospace applications, enabling designers to optimize performance and safety features of aircraft.
Another industry that benefits from CNC machining is the automotive industry. Manufacturers use CNC machines to produce components with precise dimensions and high-quality finishes. These include engine parts, transmission components, and intricate parts for electronic systems. Such precision ensures the reliable performance and durability of vehicles, a vital aspect of automotive production.
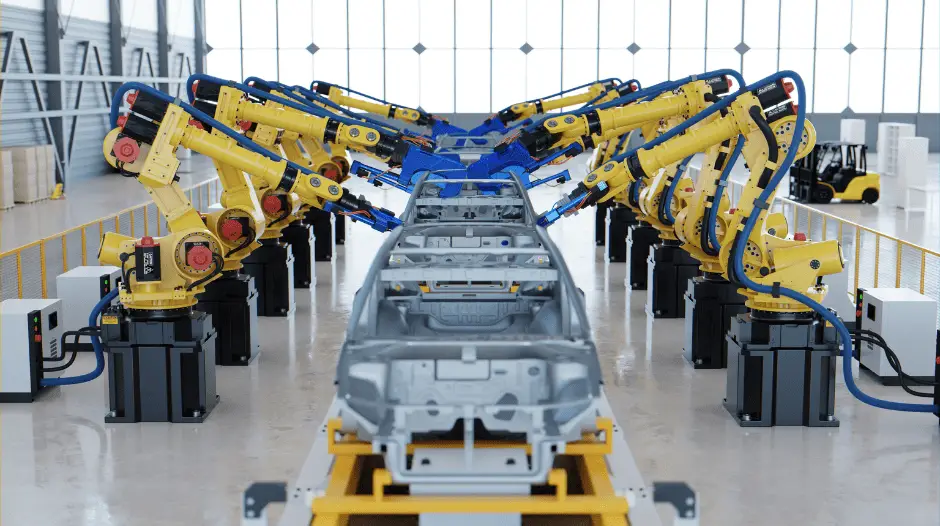
In the consumer electronics sector, CNC machining is prevalent in fabricating small and complex components that require tight tolerances. Materials like aluminum, copper, and engineered plastics are machined to produce parts for smartphones, laptops, and other electronics. This high level of accuracy ultimately contributes to devices that function well and have a long lifespan, meeting consumer expectations for quality and performance.
The defense industry also benefits from CNC machining’s capabilities, as it requires strong, lightweight, and corrosion-resistant materials for various applications. CNC machining allows the production of vital components, such as weapon systems and military vehicles’ frame parts, with high precision, ensuring operational efficiency and safety.
In the healthcare sector, CNC machines are used to produce medical components, which require accurate and high-quality finishing. Medical devices, implants, and surgical instruments often consist of complex geometries and need to adhere to stringent quality standards. With CNC machining, producers can effectively meet these requirements.
CNC machining plays a significant role in the oil and gas industry as well. Components like drilling equipment, valves, and pipes need high levels of precision and reliability to function correctly in harsh environments. CNC machined parts, made from materials such as stainless steel, hardened steel, and titanium, ensure equipment operates efficiently and withstands wear and corrosion.
Overall, CNC machining is a valuable process for producing intricate, accurate, and durable components across various industries, including aerospace, automotive, consumer electronics, defense, healthcare, and oil and gas. Its versatility, efficiency and reliability make it an essential tool in modern manufacturing.