What is CNC Machining?
CNC machining has become an integral part of various industries, as it offers precision, efficiency, and versatility when it comes to manufacturing custom parts and components. This manufacturing process has evolved from the numerical control (NC) machining process, which used punched tape cards to control machinery. CNC stands for Computer Numerical Control and refers to the automated control of machining tools, such as drills, lathes, mills, grinders, routers, and 3D printers, using a computer.
The CNC machining process involves inputting coded instructions into a computer, which translates the code into precise movements for the cutting tools. This allows factories to produce parts accurately and at a rapid pace, making it an ideal solution for intricate designs and high-volume production. CNC machines are capable of shaping a wide range of materials, including metal, plastic, wood, foam, and composite. Due to its versatility, CNC machining has been adopted by various industries, from automotive to aerospace, medical to consumer products, and many more.
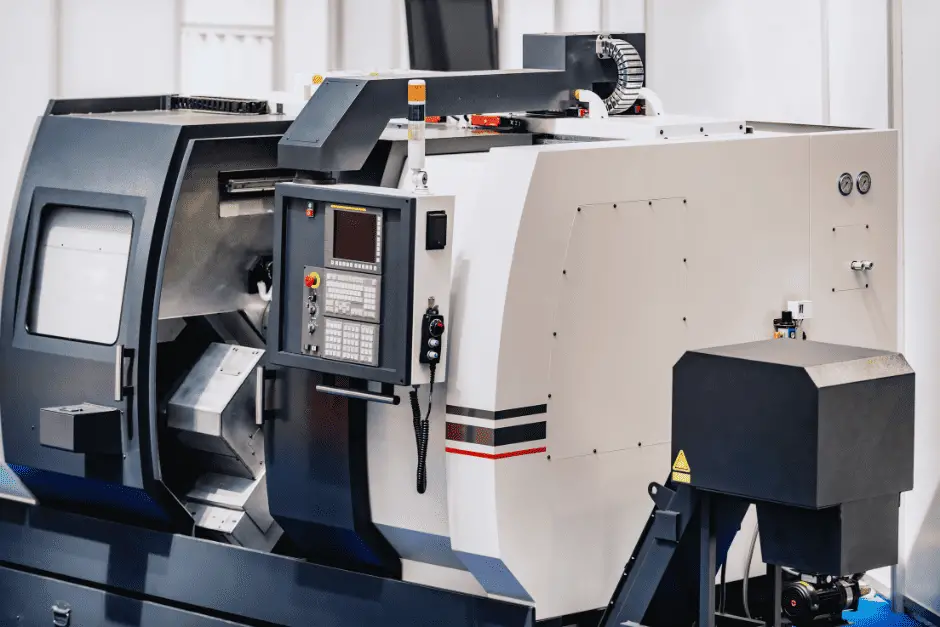
History of CNC Machining
The origins of CNC machining can be traced back to the development of numerical control (NC) machines in the 1940s and 1950s. NC machines represented a significant advancement in manufacturing technology, as they allowed for the automation of machine tools using a set of coded instructions. These instructions were typically stored on punched tape and were used to control the movements of cutting tools with increased precision and efficiency. The foundation laid by NC machines paved the way for the evolution of modern CNC machines that are widely used today.
As technology progressed, computer numerical control (CNC) emerged as an advanced form of NC machines in the 1960s and 1970s. CNC machines leveraged the power of computers to control the machining process, thereby offering a higher degree of automation and flexibility. By replacing punched tape with digital data files, the accuracy and speed of the cutting tools in CNC machines improved significantly, leading to higher productivity and reduced manual intervention.
Over the years, CNC machining has continued to undergo numerous advancements and refinements. For instance, the integration of computer-aided design (CAD) and computer-aided manufacturing (CAM) software further enhanced the capabilities of CNC machines. These technological advancements allowed for the automation of design, toolpath generation, and part programming, resulting in decreased production times and cost savings for various industries.
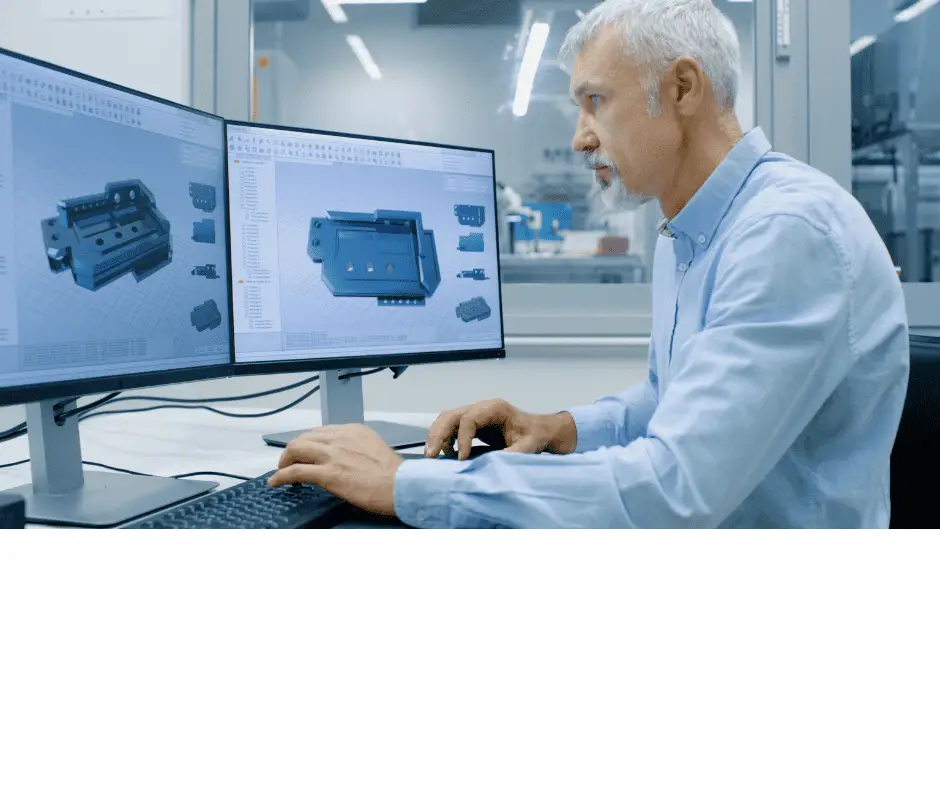
Today, CNC machining is an indispensable part of modern manufacturing, being employed across a wide range of industries such as automotive, aerospace, electronics, and medical. CNC machines have come a long way since their early beginnings as NC machines. Thanks to consistent technological advancements and innovative solutions, they continue to revolutionize the world of manufacturing, offering unparalleled precision and efficiency in the production of custom parts and designs.
Basics of CNC Machining
CNC Machines
CNC machining is a subtractive manufacturing process that employs computerized controls and machine tools to remove layers of material from a stock piece, known as the blank or workpiece, to produce a custom-designed part1. These computerized machines, called CNC machines, are capable of operating with high precision and consistency. They are used in various industries such as aerospace, automotive, and electronics.
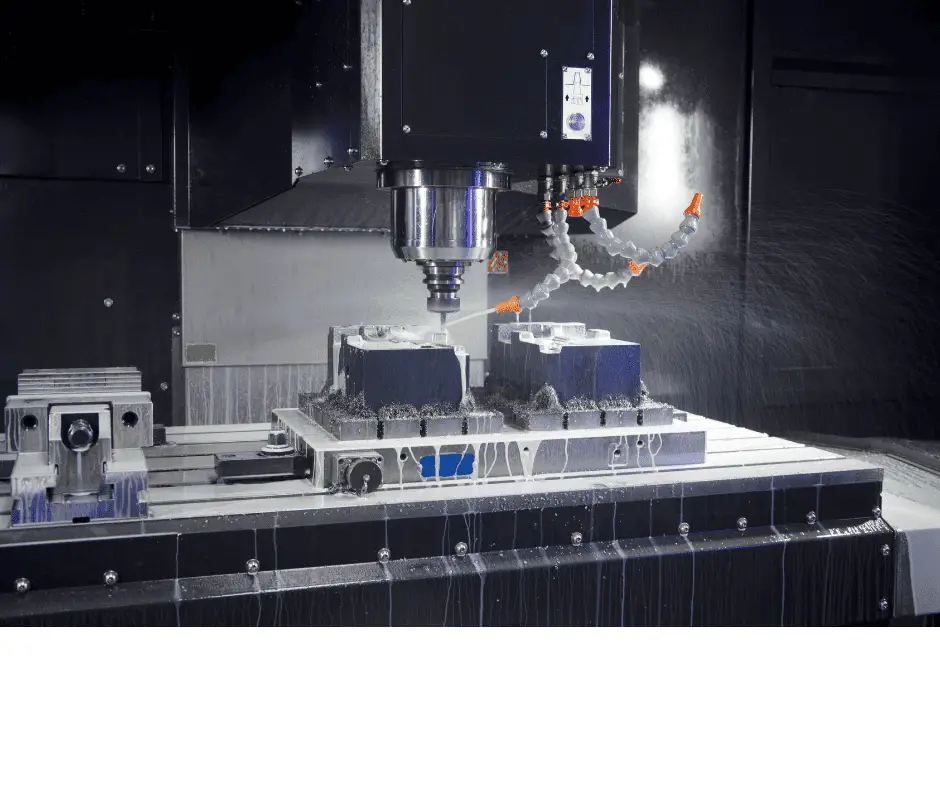
There are various types of CNC machines, each with specific capabilities and applications. Some common types include milling machines, lathes, and routers. The choice of machine depends on factors such as material, complexity of the design, and required tolerances2.
CNC Program
A critical element of CNC machining is the use of G-code and M-code programming languages. G-code provides instructions for the machine’s movements, such as linear and circular interpolation, while M-code controls additional machine functions like spindle speed and coolant flow3.
To create a CNC program, the desired part design is first developed using CAD (Computer-Aided Design) software. Then, the CAD file is imported into CAM (Computer-Aided Manufacturing) software, which translates the design into machine-readable G-code and M-code.
Once the CNC program is generated, it is loaded into the CNC machine’s computer, which then controls the movement of the cutting tool, ensuring the desired part is accurately produced4.
The following are key components of a CNC program:
- Coordinates: Define the position of the cutting tool relative to the workpiece.
- Feed rate: Determines the speed at which the cutting tool moves through the material.
- Spindle speed: Specifies the rotational speed of the cutting tool.
- Tool change: Indicates when a new cutting tool should be used.
- Coolant: Controls the application of coolant during the machining process.
This combination of computer-controlled precision and programming capabilities allows CNC machining to create complex, high-quality parts with minimal manual intervention5.
Footnotes
- What is CNC Machining? | Definition, Processes, Components & More ↩
- CNC Machining 101: Get to Know CNC Machining Basics ↩
- CNC Machining, What is it and how does it work? ↩
- What is CNC? The Complete CNC Guide for 2023 ↩
- What Is CNC Machining? The Complete Basics to Know ↩
Types of CNC Machines
CNC machining is a manufacturing process that uses computerized controls to operate and manipulate machine tools, shaping a variety of materials into custom parts and designs. There are several types of CNC machines, each with specific capabilities and applications. In this section, we will discuss some of the most common types of CNC machines, including Lathes, Mills, Routers, Grinders, Plasma Cutters, and Laser Cutters.
Lathes
CNC lathes are machines that rotate a workpiece around a stationary cutting tool, enabling precise and efficient shaping of the material. They are primarily used for turning operations and can accommodate a range of materials, including metal, plastic, and wood. The CNC Lathe Machine manages and transfers material programmatically to the computer, allowing for a high degree of precision and customization.
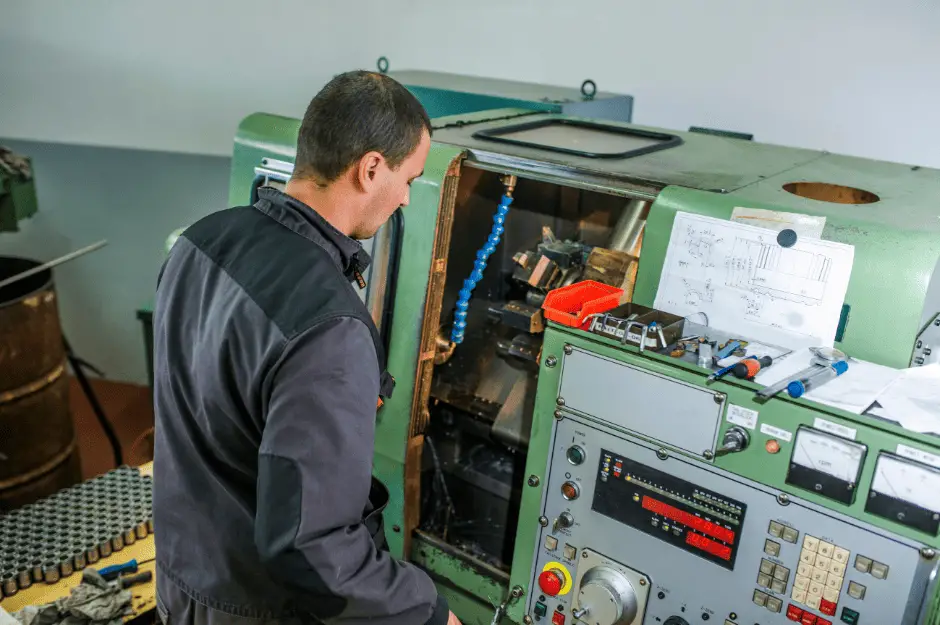
Mills
CNC milling machines utilize a rotating cutting tool to remove material from a stationary workpiece. They can perform a variety of operations, such as drilling, tapping, and boring, to create a custom part. With the ability to operate on multiple axes, CNC mills offer a high level of versatility for applications ranging from aerospace components to medical devices.
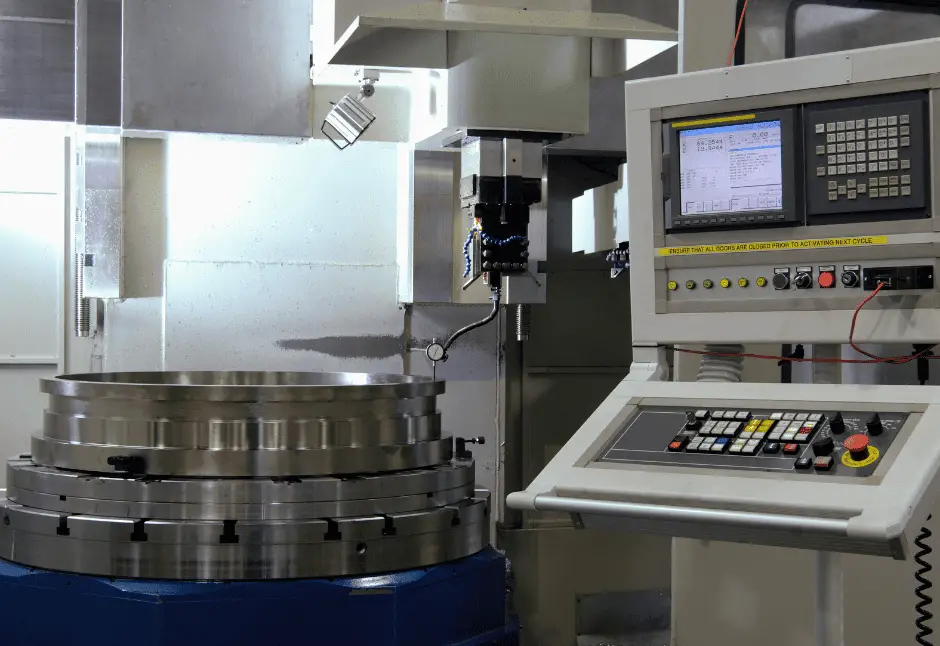
Routers
CNC routers are similar to milling machines but are typically less expensive and designed for cutting softer materials such as wood, plastic, and foam. These machines can create intricate shapes and designs in a variety of industries, from cabinetry to sign making. Some lower-cost CNC routers also cater to hobbyists and smaller businesses, making them accessible to a wider audience.
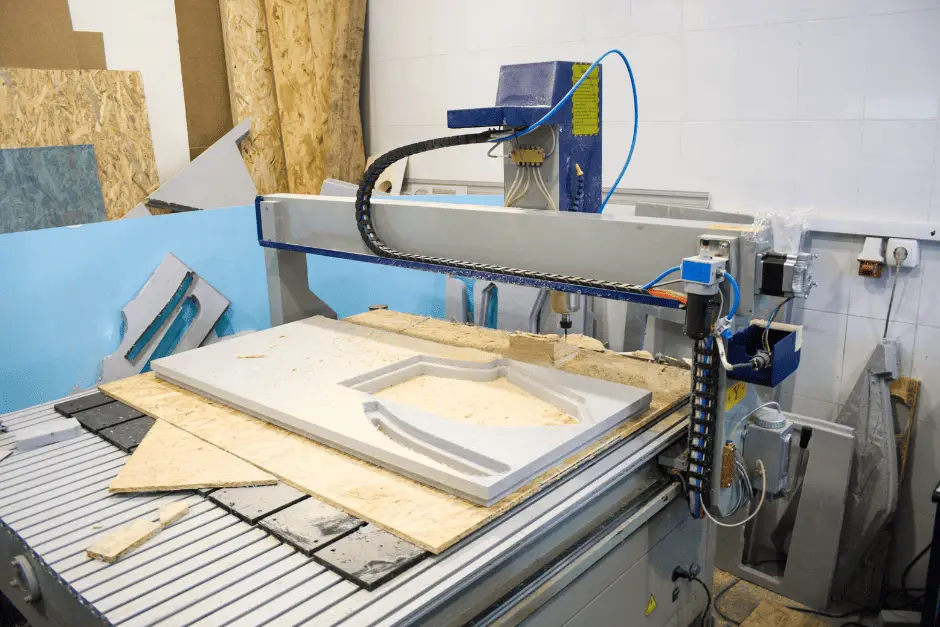
Grinders
CNC grinders use a rotating abrasive wheel to shape and finish workpieces through accurate, high-precision grinding. These machines are particularly well-suited for creating precision components with tight tolerances, such as cutting tools, automotive parts, and aerospace components. With various types of grinders available, manufacturers can select the ideal machine for specific grinding applications.
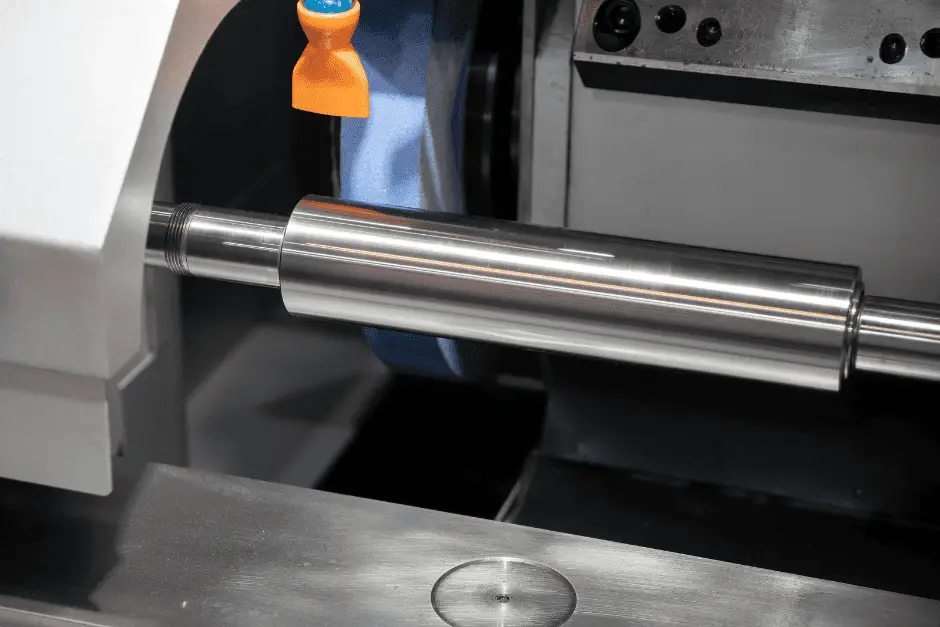
Plasma Cutters
CNC plasma cutters use a high-velocity jet of ionized gas to cut through electrically conductive materials. These machines provide accurate, efficient cutting, especially for thick materials like steel or aluminum. Plasma cutters are often used in industrial settings, like shipbuilding and manufacturing, due to their ability to produce large, intricate shapes with minimal waste.
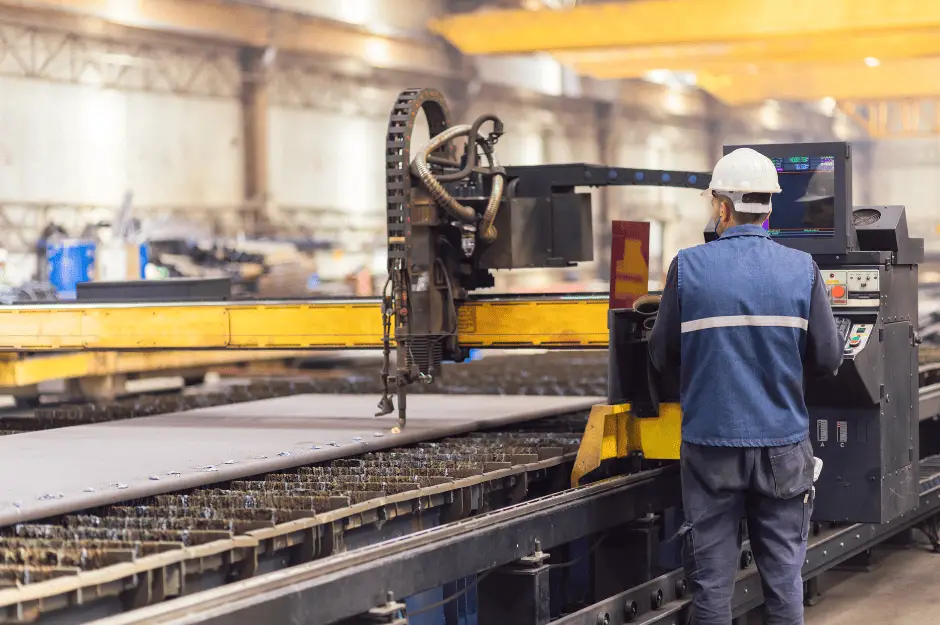
Laser Cutters
Laser cutters use a focused laser beam to slice through materials with precision and accuracy. They are ideal for cutting thin materials such as sheet metal, plastic, or wood, and can produce intricate shapes with minimal kerf (the width of the cut). CNC laser cutters are used in various industries, from electronics to automotive manufacturing, thanks to their ability to produce highly detailed designs.
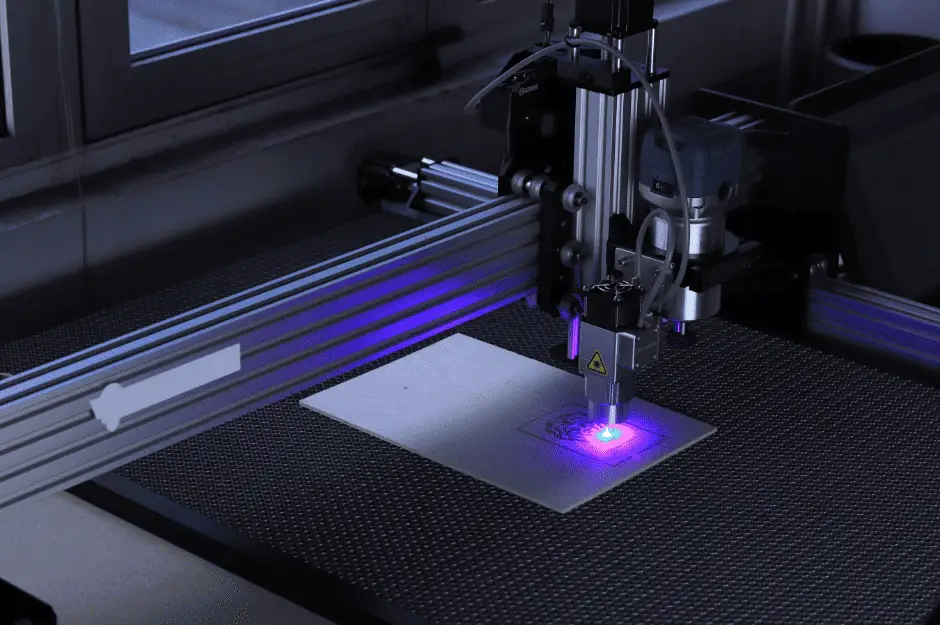
Materials and Tools
Cutting Tools
CNC machining utilizes a wide variety of cutting tools for different operations. These tools range from end mills to thread mills, enabling CNC machines to conduct a wide range of cuts and incisions in a component. The choice of cutting tool depends on the material being machined and the desired outcome of the process. Some common types of cutting tools include:
- End mills: Used for various milling operations and available in different shapes and sizes.
- Drills: Employed for creating holes in the material.
- Taps: Utilized for threading operations.
Materials Used
CNC machining can work with a diverse range of materials, from metals and plastics to wood, foam, and composite materials. Each material has its own unique properties, which can influence the choice of cutting tools and machining parameters. Some common materials used in CNC machining are:
- Metals: This category includes materials such as aluminum, brass, and steel. These are often chosen for their strength and durability. Aluminum is widely used due to its lightweight and versatility, while brass is popular for its corrosion resistance and ease of machining.
- Plastics: Materials like nylon and acrylic are commonly machined using CNC due to their favorable properties, such as resistance to wear and impact. Plastic materials can be easily shaped into custom parts and designs.
- Wood: CNC machines can also work with wood materials, offering precise cuts and finishes for various applications.
- Foam: Expanded polyurethane foam is an example of a material that can be CNC machined, as it is lightweight and can be easily shaped.
- Composites: Materials such as fiberglass and carbon fiber composites can be machined using CNC. These materials offer a unique combination of strength and lightness, making them ideal for various industries.
In conclusion, the versatility of CNC machining allows for a wide range of materials and cutting tools to be used. This flexibility enables industries to manufacture custom parts and designs for diverse applications, catering to different material requirements and specifications.
Manufacturing Process
CNC machining, or Computer Numerical Control machining, is a versatile manufacturing process that shapes stock material into custom parts and designs based on computer-generated instructions. There are various manufacturing processes that are encompassed within CNC machining, including subtractive, additive, and formative manufacturing. In this section, we will discuss each of these processes and their role in producing parts with high precision, automation, and repeatability.
Subtractive Manufacturing
Subtractive manufacturing is a process that removes material from a stock piece to create the desired part, based on predetermined specifications. This usually involves milling, turning, or cutting the original material to achieve a precise and accurate geometry. CNC machining can handle various materials, such as metals, plastics, wood, and foam, making it widely applicable across industries. The automated nature of the process ensures high levels of repeatability and accuracy while minimizing human intervention. For more information on CNC milling, visit Dassault Systèmes’ article on the milling process.
Additive Manufacturing
While not a traditional CNC process, additive manufacturing, commonly known as 3D printing, complements subtractive manufacturing by enabling the creation of complex geometries that may be challenging to achieve with subtractive methods alone. In additive manufacturing, material is added layer by layer to form a part, using computer-aided design (CAD) models as a guide.
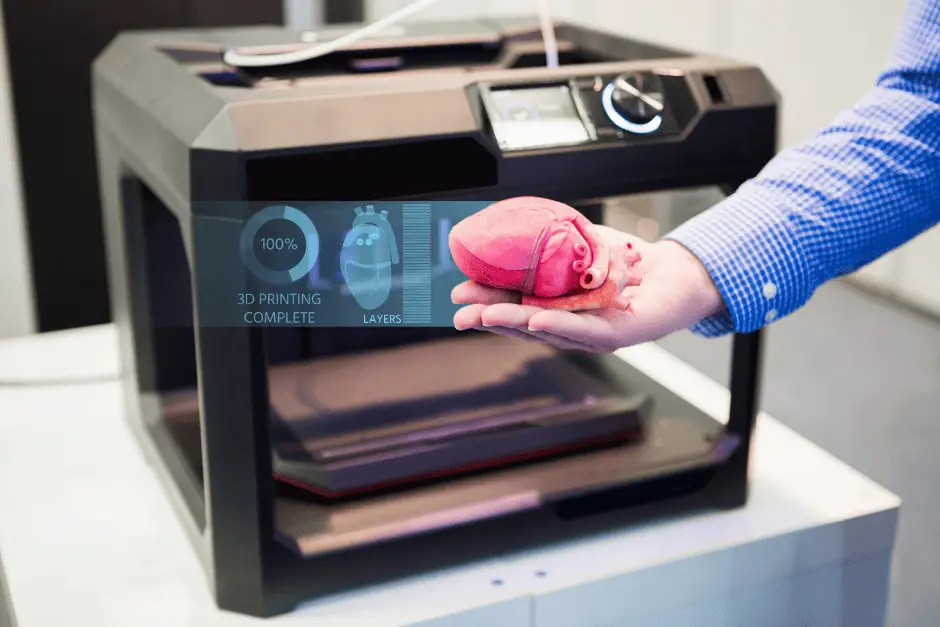
This process is particularly useful for producing intricate designs and prototypes that would otherwise require specialized tooling. Although additive manufacturing is a separate process from CNC machining, it shares the computerized control aspect, allowing for seamless integration in manufacturing workflows.
Formative Manufacturing Process
Formative manufacturing processes, such as injection molding, are a part of the broader CNC capabilities. In these processes, material is formed into the desired shape by applying heat, pressure, or a combination of both. Injection molding, for instance, involves melting plastic and injecting it into a mold to create the final part. The CNC controls maintain the necessary parameters to ensure consistency and repeatability. Formative manufacturing is suitable for mass production, coupled with the ability to maintain tight tolerances and produce a wide range of part designs.
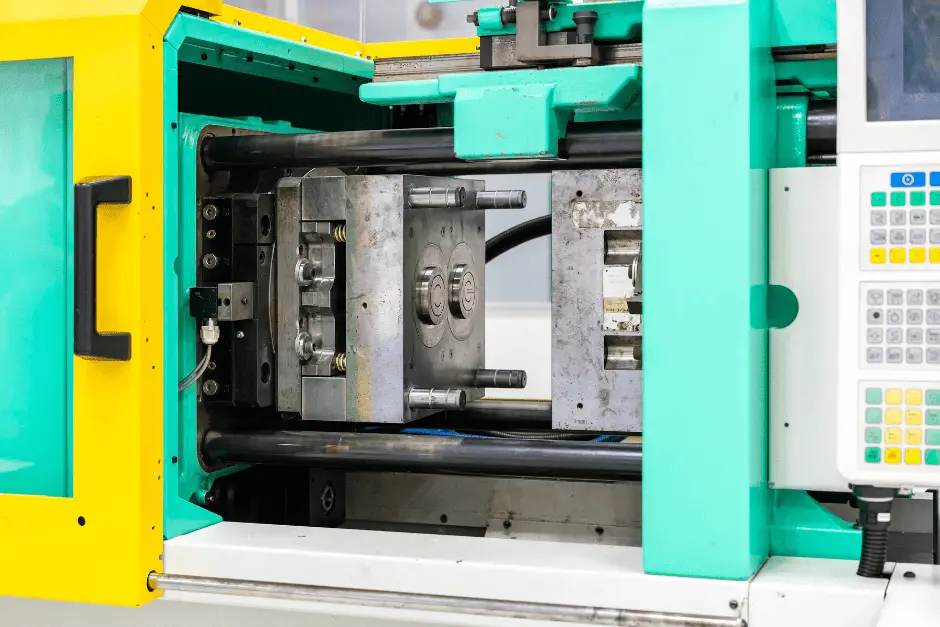
In summary, CNC machining encompasses a variety of manufacturing processes that cater to different needs within the industry. Subtractive, additive, and formative processes offer distinct advantages while working together to create versatile and precise parts with confidence and ease.
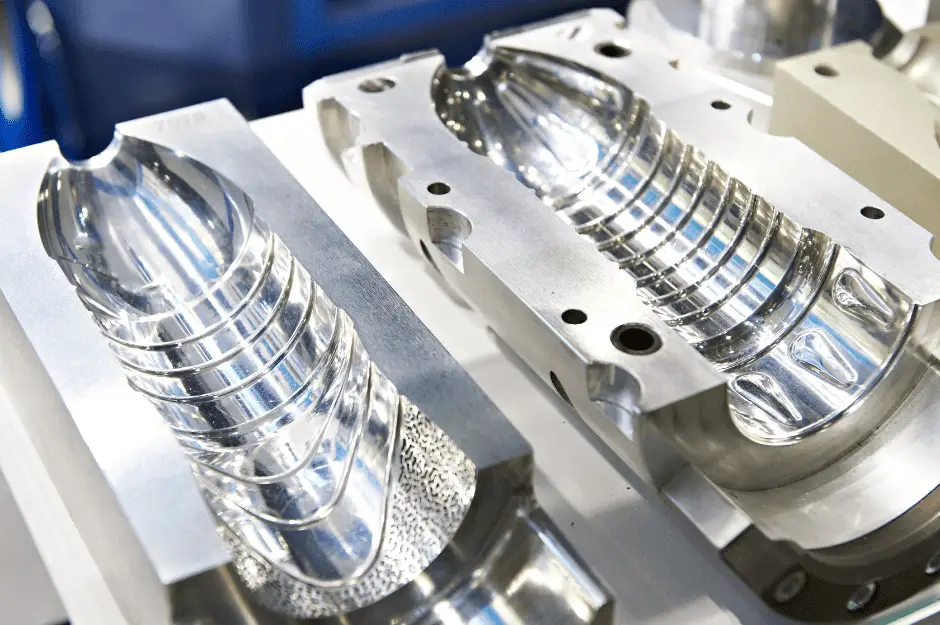
Comparison to Other Manufacturing Techniques
In this section, we will compare CNC machining to another popular manufacturing technique, 3D printing, to help you understand their key differences and potential applications.
CNC vs 3D Printing
CNC (Computer Numerical Control) machining and 3D printing are both widely used manufacturing processes. However, they utilize different methods in creating parts and components.
CNC Machining is a subtractive manufacturing technology, where material is removed from a solid block, or workpiece, using various CNC machining equipment such as milling machines, lathes, and grinders. This process is known for its high precision and versatility in creating a wide range of materials, including metal, plastic, wood, foam, and composites.
3D Printing, on the other hand, is an additive manufacturing technology, where material is built up layer by layer to create a part, following a digital model. 3D printing works with a variety of materials like plastics, metals, and even biocompatible substances.
Below are some key considerations when comparing CNC machining and 3D printing:
- Speed: CNC machining is often faster for producing metal parts, as it can remove material more quickly than 3D printing can build them. For small-scale production and prototyping of plastic parts, 3D printing can be faster due to its layer-by-layer approach.
- Complexity: 3D printing can create highly complex and intricate geometries that may be difficult or impossible to achieve with CNC machining. However, CNC machining can achieve tighter tolerances and higher precision in comparison to 3D printing.
- Finish: CNC machined parts typically have a smooth finish, while 3D printed parts may require post-processing to achieve a comparable surface finish.
- Cost: The total cost of production depends on various factors like material, part complexity, and production volume. For low-volume production and prototypes, 3D printing can be more cost-effective, while CNC machining can be more suitable for producing larger quantities and parts with tighter tolerances.
In conclusion, both CNC machining and 3D printing have their advantages and limitations, and selecting the appropriate process for a particular application depends on factors like material, production volume, and part complexity.
Industry Applications
Aerospace
The aerospace industry extensively uses CNC machining for the production of complex and high-precision components. Aerospace parts often require custom manufacturing processes and materials, making CNC machining an ideal choice for producing these parts. CNC turning and milling operations help create intricate shapes, such as turbine blades and engine components, using materials like aluminum, titanium, and other advanced alloys. CAD and CAM software are used to design and program the CNC machines, ensuring that each component meets stringent tolerances and quality standards.
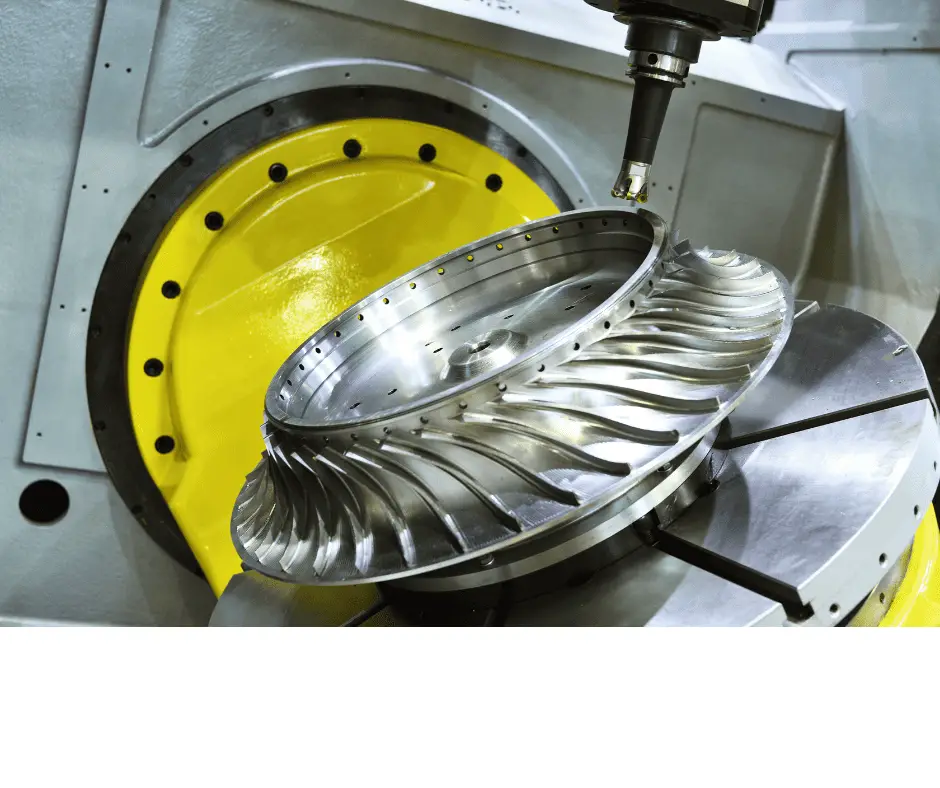
Automotive
In the automotive industry, CNC machining plays a significant role in manufacturing engines, transmissions, and other critical systems. Car manufacturers turn to CNC machining for its ability to produce high volumes of consistent and complex parts from materials such as steel, aluminum, and plastics. Precision is crucial in automotive production, as even slight variations in components can result in performance issues or system failures. CAM and CAD software help engineers design and manufacture parts that meet the exacting specifications required by the automotive industry.
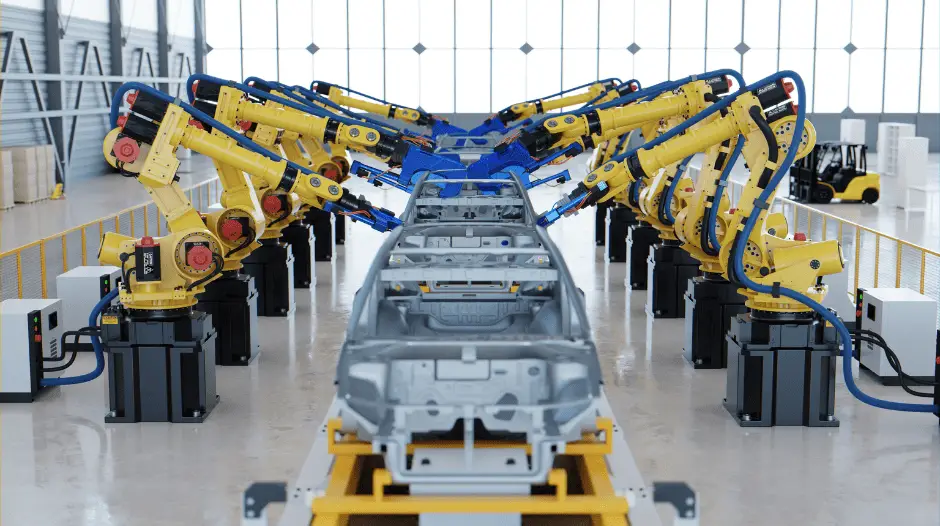
The stock photography is from Canva.
Medical
CNC machining is widely used in the medical industry to produce various medical devices and equipment, including surgical instruments, implants, and prosthetics. The versatility of CNC machining materials enables manufacturers to work with diverse materials such as stainless steel, titanium, and plastics. These materials are often needed for their biocompatibility, strength, and corrosion resistance. The high degree of precision and repeatability offered by CNC machining ensures that medical components are produced within strict tolerances, reducing the risk of human error and ensuring patient safety.
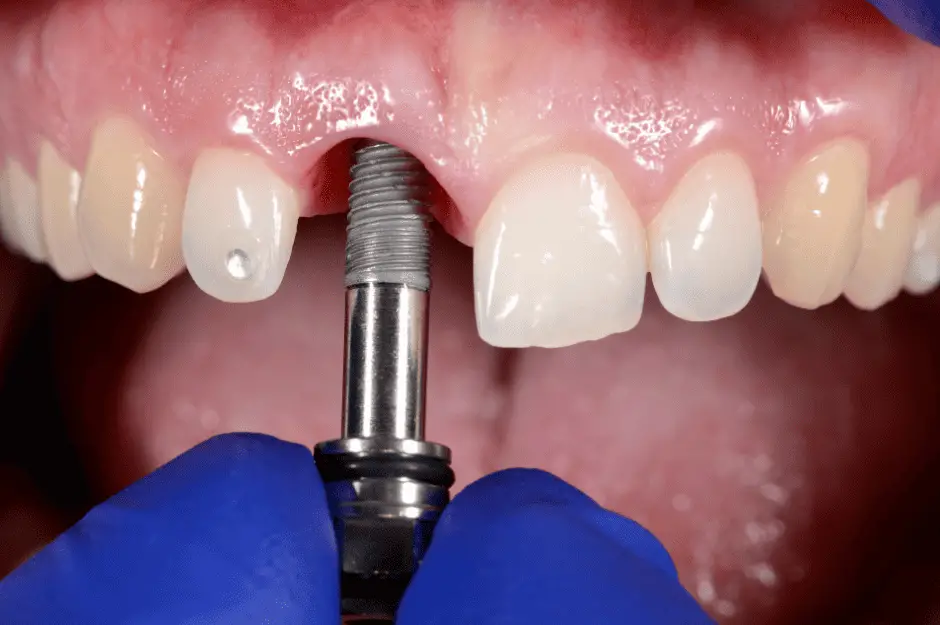
Electronics
The electronics industry relies on CNC machining for the production of parts and components that make up various consumer and industrial electronics devices. CNC machining is utilized to create circuit boards, housings, connectors, and other critical components that require high precision and intricate designs. The ability to work with a range of materials, such as aluminum, plastics, and copper, enables manufacturers to produce components optimized for electrical conductivity, heat dissipation, and durability. With the aid of CAD and CAM software, CNC machining supports the efficient, consistent, and accurate production of electronic components to meet industry demands.
Advantages and Disadvantages of CNC Machining
Precision and Accuracy
CNC machining offers high precision and accuracy in manufacturing custom parts and components. This is due to the computerized controls that guide cutting tools to shape stock material with high tolerances. This leads to an increased production of quality parts with comparatively fewer errors compared to manual machining processes. The machines are capable of maintaining a consistent production level, resulting in less waste and reduced cost.
Speed and Scalability
One of the main advantages of CNC machining is its speed and scalability. The process is faster than manual machining due to the automation of milling, turning, or EDM machines. This efficiency allows for the quick production of parts, making it ideal for prototyping or medium-scale production. Moreover, CNC machines can easily produce multiple identical parts with consistency, making the process scalable as production needs increase.
The disadvantages of CNC machining are mainly related to its high upfront costs. Firstly:
- Expensive Machinery: The initial cost of CNC machines can be prohibitive for some businesses. Additionally, maintenance costs can be high, further increasing overall expenses.
Despite its advantages, CNC machining also has some limitations and drawbacks:
Complexity and Limitations
- Limited materials: The material selection for CNC machines is not as extensive as that for conventional machining tools. Predominantly, metal materials can be processed, restricting the range of materials and, subsequently, the applications of CNC machining.
- Complexity: While CNC machines can handle complex geometries and designs, part complexity can affect production time and costs. As the complexity of a part increases, the time spent on setting up and programming the machine also increases, leading to longer lead times and potentially higher costs.
In summary, CNC machining is a useful manufacturing process that offers advantages in terms of precision, accuracy, speed, and scalability. However, it is essential to weigh these benefits against the high costs and material limitations to determine if it is the right approach for specific manufacturing needs.
Preparing for CNC Machining
CAD Models
CNC machining starts with creating a CAD model, which is a computer-aided design of the intended part. A CAD model is created using specialized software, and it represents the geometric design of the object to be machined. These CAD files are essential in the CNC machining process, as they serve as the blueprint for the programmable machine to follow. The model must be accurate and reflective of the desired final product, as it determines the dimensions and measurements that the CNC machine will work with.
When creating a CAD model, designers should consider the material to be used, as well as the necessary tolerances and cutting requirements. It is crucial to ensure the model is designed with manufacturability in mind, taking into account any potential challenges that may arise during the CNC machining process.
CAM Programming
After finalizing the CAD model, the next step in preparing for CNC machining is CAM (Computer-Aided Manufacturing) programming. This process involves converting the CAD file into a set of instructions for the programmable machine to follow. The CAM software is a crucial component of CNC machining, as it translates the design data into a language that the CNC machine can understand and autonomously execute.
To achieve this, CAM programming employs different algorithms and tools to generate a set of G-code instructions. G-code is the standard programming language used by CNC machines to control and coordinate their movements throughout the machining process. These instructions guide the machine in terms of the spindle speed, cutting tool paths, feed rates, and other essential parameters.
The CAM programming process needs to be done with precision and care, as errors in the generated G-code can result in machining faults or damages to the CNC machine. Proper preparation and optimization of the CAM program are crucial to achieving high-quality and accurate CNC machined parts.
Workpiece in CNC Machining
One-off
In CNC machining, a workpiece is the material that is shaped or modified to create the final product. One-off workpieces are unique pieces created specifically for a single project or product. These workpieces are programmed with a CNC program and can involve the use of various tools such as drills, mills, and shafts to create intricate designs and complex geometries. CNC machining is adept at handling one-off projects due to its precision and ability to customize the final product.
Stock Material
Stock material serves as the initial form of the workpiece before it undergoes CNC machining processes. Common stock materials include metals, plastics like ABS, and even wood. The choice of stock material depends on the desired properties of the final product, such as strength, durability, and aesthetics. CNC machining can work with a wide range of materials, making it a versatile manufacturing process. For example, gears can be machined from metals for high-stress applications, while plastic or wooden workpieces can be used for more aesthetic or lower-stress projects.
Part Geometries
CNC machining facilitates the creation of various part geometries with high precision and accuracy. Complex shapes and designs can be achieved through different CNC machining techniques. In addition to traditional milling and drilling, other methods such as laser cutting, spinning, and pinning can be used to create the desired part geometry.
Laser cutting, for instance, is ideal for producing intricate designs with a high level of accuracy. Spinning is a technique typically used for creating axisymmetric parts like shafts, whereas pinning is employed for joining parts together without the use of additional fasteners or adhesives.
CNC machining’s flexibility allows for the production of various part geometries according to the specific requirements of different industries and applications. Incorporating these techniques into the CNC machining process results in a diverse range of end products with precise dimensions and intricate details.
CNC Machining Parameters
Cutting Speed
The cutting speed is a crucial parameter in CNC machining as it directly impacts the efficiency, surface finish, and tool life. Cutting speed refers to the speed at which the cutting tool engages the material being machined. It is measured in surface feet per minute (SFM) or meters per minute (m/min). Choosing the optimal cutting speed ensures that the machining process is both efficient and results in high-quality surface finishes. Moreover, using the appropriate cutting speed helps extend the life of the cutting tool, reducing the overall cost of production.
Feed Rate
Feed rate is another essential parameter in CNC machining. It refers to the linear distance the cutting tool travels in relation to the workpiece for every revolution of the spindle. This parameter is typically measured either in inches per minute (IPM) or millimeters per minute (mm/min) and plays a significant role in surface finish quality and productivity. A higher feed rate can help to remove material more quickly, thus reducing the machining time. However, setting the feed rate too high might cause excessive tool wear or breakage, leading to potential damages to the workpiece. Therefore, it’s crucial to find a balance between these factors to achieve the desired results.
Location
In CNC machining, the location parameter accounts for the position of the cutting tool in relation to the workpiece. A CNC program is responsible for controlling the location of the cutting tool with a high level of precision and accuracy. This is essential for intricate and complex machining tasks such as engraving or creating printed circuit boards. Accurate control of location parameters ensures that the final product meets the required dimensions and tolerances.
To summarize, optimizing the parameters of cutting speed, feed rate, and location is critical in CNC machining. These factors contribute to increased efficiency, improved surface finish, and prolonged tool life, making the process more durable and cost-effective overall.
Frequently Asked Questions
What are the common operations in CNC machining?
CNC machining is a subtractive manufacturing process that employs computerized controls and machine tools to remove layers of material from a stock piece, producing a custom-designed part. Common operations in CNC machining include milling, turning, drilling, and grinding. These processes involve the precise removal of material using various cutting tools to achieve the desired shape and dimensions.
How does CNC machining differ from manual machining?
CNC machining differs from manual machining due to its automation and precision. Manual machining relies on a human operator to directly control the machine tools, whereas CNC machining uses pre-programmed computer software to dictate the movement of factory tools and machinery. CNC machines also offer greater accuracy and can handle more complex tasks due to their ability to perform three-dimensional cutting operations in a single set of prompts.
What industries commonly use CNC machines?
CNC machines are widely used in various industries, including aerospace, automotive, medical, electronics, and manufacturing. Their flexibility and adaptability make them ideal for producing custom metal and plastic parts with tight tolerances and intricate geometries. They are also commonly used for rapid prototyping and small-batch production runs, making them an essential tool for many different applications.
What materials can be processed using CNC machining?
CNC machines are capable of processing a wide range of materials, including metals, plastics, wood, foam, and composites. Some common metals used in CNC machining are aluminum, steel, brass, and copper, while plastics like ABS, polycarbonate, and nylon are also easily machined with CNC technology. The choice of material depends on the specific application and desired performance characteristics of the final part.
How do CNC machinists interpret design specifications?
CNC machinists interpret design specifications using CAD (Computer-Aided Design) models. These digital representations of a part provide the necessary dimensions, tolerances, and other design details. The machinist then converts the CAD model into a set of instructions, known as G-code, which the CNC machine uses to control its movements and execute the desired machining operations.
What factors affect the accuracy of CNC machining?
Several factors affect the accuracy of CNC machining, including the machine’s stiffness, the quality and sharpness of the cutting tools, the part’s material properties, and the machining process parameters, such as cutting speed and feed rate. Proper maintenance of the machine, regular calibration, and skilled programming can help minimize errors and maintain high levels of precision in the final part.