A CNC operator plays a vital role in the manufacturing industry, responsible for producing machined parts using computer numerical control (CNC) machines. These machines transform raw materials into precision parts based on specific designs, contributing to the creation of a wide variety of products. CNC operators require advanced technical skills, strong attention to detail, and the ability to adhere to strict safety standards.
CNC operators program, set up, and operate CNC machines, which use computer-aided design (CAD) and computer-aided manufacturing (CAM) software to cut, shape, and form various materials. These professionals work in a variety of industries, including automotive, aerospace, and electronics, among others. As an entry-level position, CNC operators often receive on-the-job training and can progress into more specialized roles, such as CNC machinists or programmers, as they gain experience.
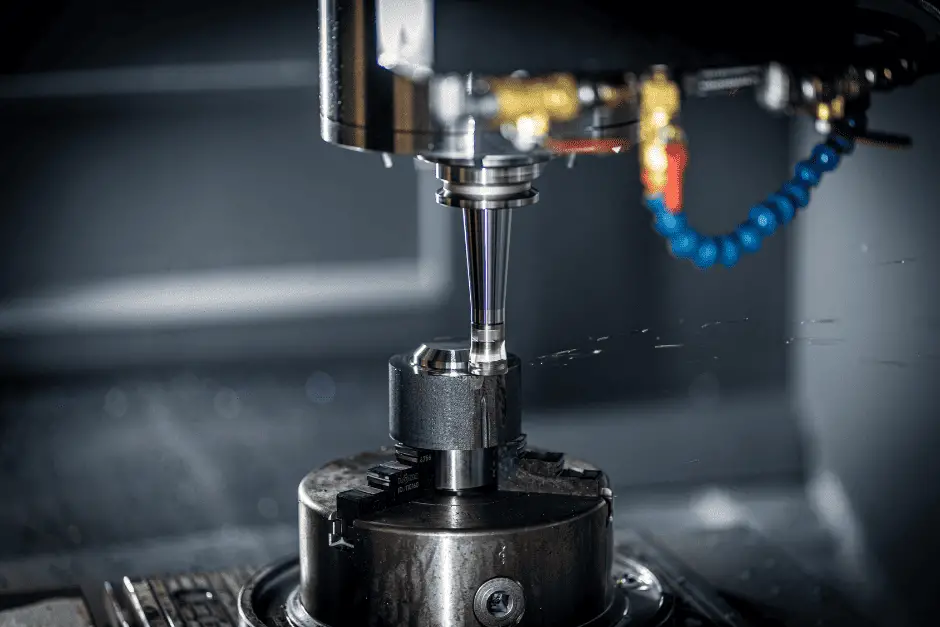
In addition to operating CNC machines, a CNC operator is responsible for maintaining the equipment, ensuring that it adheres to quality and safety standards. This includes performing routine maintenance, troubleshooting issues, and making necessary adjustments to the machine and its programming. By diligently performing these tasks, CNC operators play a crucial role in ensuring the production process runs smoothly and efficiently.
Roles and Responsibilities
CNC Setup
A CNC operator is responsible for preparing and setting up CNC machines for operation. This process involves reading blueprints and mechanical drawings to understand the specifications of the task at hand. They calibrate the equipment using proper procedures and ensure that the correct tools and materials are loaded and unloaded for production.
Operating CNC Machines
Once the machine is set up, the CNC operator is responsible for operating the CNC machine, starting and stopping it as required. They translate instructions into computer commands so the machines perform the correct tasks, such as drilling, grinding, and milling. Operators also oversee the production process, making adjustments and minor repairs as needed to ensure the smooth operation of the machinery.
Quality Control and Inspection
CNC operators play a crucial role in maintaining the quality standards of finished products. They inspect each part produced by the CNC machine, using measuring tools and devices to check dimensions and tolerances. They also monitor the production process closely to identify any deviation from the specifications, making necessary adjustments to bring the process back on track. Ensuring the accuracy and quality of the final product is an important responsibility for the CNC operator.
Maintenance and Troubleshooting
Regular maintenance is an essential aspect of a CNC operator’s duties, helping to prevent breakdowns and ensure the longevity of the machinery. CNC operators are tasked with performing routine maintenance checks, such as lubricating and cleaning the equipment, as well as identifying any potential issues that may arise during operation. When problems do occur, operators must troubleshoot and resolve the issue, either by conducting repairs themselves or under the supervision of a more experienced machinist.
In summary, a CNC operator is responsible for setting up, operating, and maintaining CNC machines while ensuring the production of high-quality parts. This involves calibrating equipment, loading and unloading tools and materials, monitoring the production process, performing inspections, and troubleshooting any issues that arise.
Skills and Abilities
Programming
A CNC operator should be proficient in programming and using Computer-Aided Manufacturing (CAM) software. They need to stay up-to-date on the latest software and tools to efficiently make parts when given a G-code program.
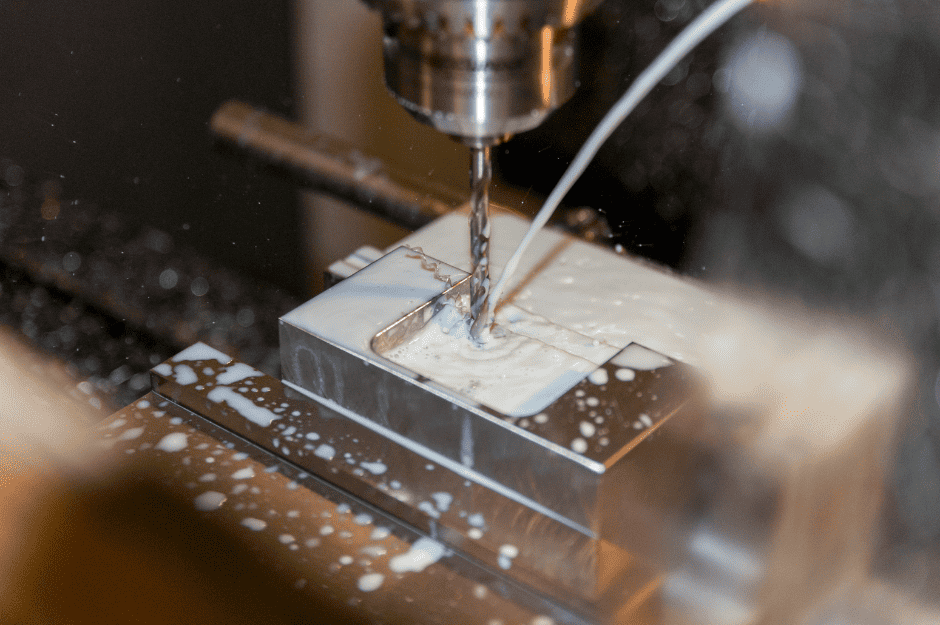
Attention to Detail
CNC operators must have a keen eye for detail since they are responsible for setting up work offsets, tool length offsets, inspecting parts, and deburring. Ensuring accuracy and precision is essential for the manufacturing process.
Problem Solving
CNC operators need strong problem-solving skills. They should be able to troubleshoot and resolve issues such as crashes, tool wear, and machine malfunctions. Additionally, they should be adept at optimizing program performance for higher efficiency.
Mechanical Aptitude
A good understanding of machines and their capabilities is crucial for a CNC operator. They should be familiar with the machinery’s mechanical components to ensure smooth operation and maintenance.
Analytical Skills
Analytical skills are essential for a CNC operator, as they need to read and understand part drawings, blueprints, models, and other technical specifications related to their craft. They must analyze data and make necessary adjustments to maintain the quality of produced components.
Technical Drawing
CNC operators should have a strong foundation in technical drawing, as they often work with blueprints and part specifications. They must be able to interpret and analyze these drawings to set up the machines and create the required components.
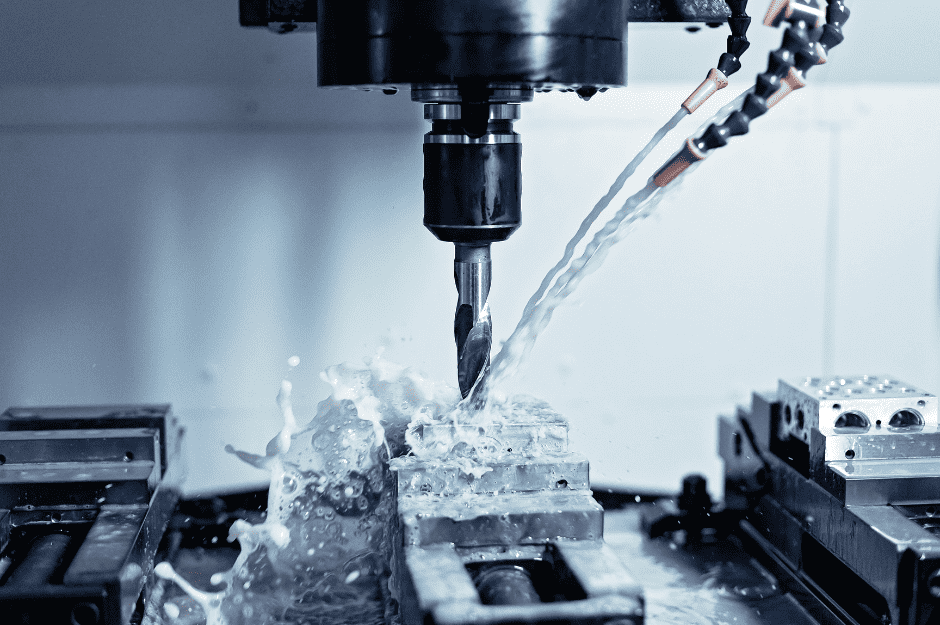
Overall, a CNC operator’s skills and abilities are crucial for ensuring efficient and accurate manufacturing processes. By mastering programming, attention to detail, problem-solving, mechanical aptitude, analytical skills, and technical drawing, they can effectively operate and maintain CNC machines.
Education and Training
Educational Requirements
CNC operators typically require a high school diploma or equivalent as their minimum educational requirement. However, many operators attend post-secondary programs, such as trade schools or community colleges, to gain further knowledge and skills in the field. These programs often focus on subjects like math, blueprint reading, and computer-aided manufacturing (CAM) software.
Certifications
Although not always required, there are several certifications available for CNC operators to enhance their skills and job prospects. For example, the National Institute for Metalworking Skills (NIMS) offers various industry-recognized credentials. Additionally, equipment manufacturers like Haas Automation have their certification programs that focus on the safe and efficient operation of specific CNC machines.
Apprenticeship and On-the-Job Training
Many CNC operators gain practical experience through apprenticeships or on-the-job training programs, which allow them to learn the trade under the guidance of experienced professionals. These programs can range from a few months to a couple of years, depending on the employer and the level of expertise required. On-site training is an integral part of developing a CNC operator’s skills, as it allows them to apply classroom knowledge to real-world scenarios.
Continuing Education
As technology evolves, it is essential for CNC operators to stay up-to-date with advancements in their field. This can be achieved through continuous learning opportunities, such as:
- Attending workshops and seminars organized by industry associations, like the Fabricators & Manufacturers Association.
- Participating in online courses or certification programs that cover updates on CAM software or new machining techniques.
- pursuing advanced degrees or diplomas in related fields, such as engineering or manufacturing management.
Overall, a well-rounded, ongoing education and training plan will prepare CNC operators to excel in the constantly evolving manufacturing landscape.
CNC Machining Techniques
CNC machining is a widely used manufacturing technique that incorporates computer-controlled processes to create precise parts and components. This section focuses on four main CNC machining techniques: milling, drilling, grinding, and turning.
Milling
Milling is a versatile CNC machining technique that involves removing material from a workpiece by utilizing a rotating cutting tool, called a mill. The process can be performed on both horizontal and vertical axes, allowing for a wide range of shapes and sizes to be produced. Some common milling operations include:
- Face milling: for producing flat surfaces or finishing a workpiece
- Peripheral milling: for shaping the edges of a part
- Pocket milling: for creating cavities or recesses in the workpiece
- Skin milling: for refining the surface finish
Milling machines can utilize various tools depending on the needs of the project, including end mills, ball mills, and slab mills, among others.
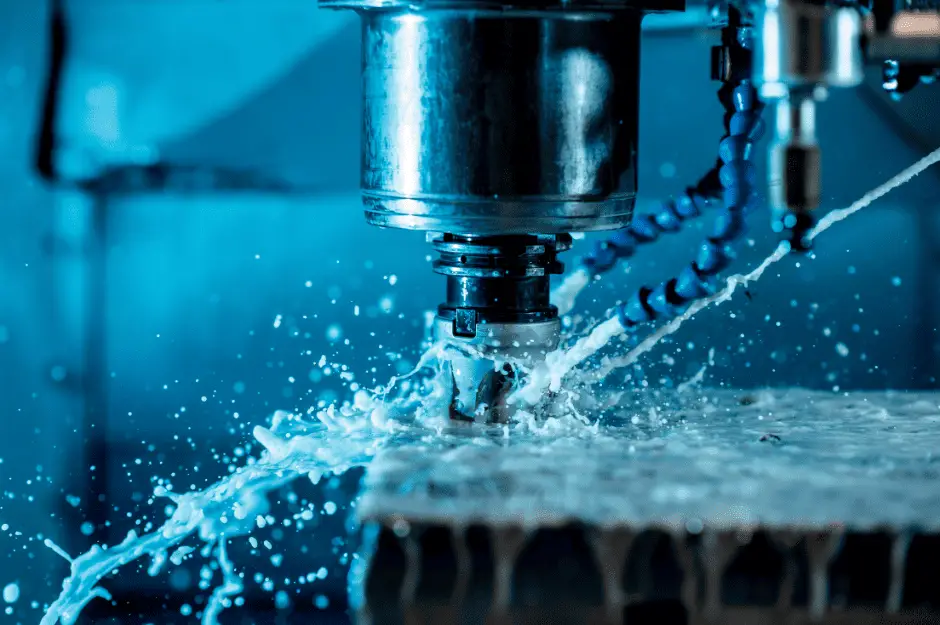
Drilling
Drilling is a CNC machining process that creates holes in a workpiece using a rotating cutting tool called a drill. This operation can be performed across a wide range of materials and is essential for creating components with specific features or functions. Drilling techniques include:
- Spot drilling: for accurate hole positioning
- Deep hole drilling: for creating extensive holes in the workpiece
- Counterboring: for enlarging or finishing an existing hole
Drilling processes can be performed using multiple spindle machines or specialized drill presses, depending on the complexity and precision required.
Grinding
Grinding is a precise CNC machining technique that uses an abrasive wheel to remove material from a workpiece’s surface. The process achieves a high level of accuracy and surface finish, making it ideal for finishing operations or producing delicate components. Grinding operations include:
- Surface grinding: for refining flat surfaces
- Cylindrical grinding: for finishing cylindrical components
- Creep-feed grinding: for processing intricate contours or profiles
Grinding machines can feature various wheel types, including straight, cup, and dish wheels, offering the flexibility to achieve a range of desired outcomes.
Turning
Turning is a CNC machining technique that involves the rotation of a workpiece against a stationary cutting tool, such as a single-point turning or a multi-point cutting tool. The process is performed on a lathe, a machine tool designed for shaping materials through cutting, sanding, or other operations. Turning can produce a variety of shapes and sizes, including straight, tapered, and contoured profiles. Some common turning operations include:
- Facing: for creating a flat surface or reducing the length of the workpiece
- Taper turning: for producing tapered surfaces or profiles
- Grooving: for cutting recesses or grooves into the workpiece
Turning machines come in various configurations, such as manual, semi-automatic, and CNC lathes, depending on the level of complexity and precision required.
Tools and Equipment
A CNC operator works with various tools and equipment to produce machined parts while adhering to quality and safety standards. This section will discuss the common tools and equipment used by CNC operators, such as calipers, micrometers, and the importance of following safety guidelines.
Measurement Tools
CNC operators rely on precise measurement tools to ensure the accuracy of machined parts. Two essential tools for this purpose are:
- Calipers: These versatile measuring instruments come in different varieties, such as digital and dial calipers. Calipers can measure inside, outside, depth, and step dimensions and can be highly accurate depending on the quality and care of the operator.
- Micrometers: Slightly more accurate than calipers, micrometers are essential for measuring small dimensions, up to one ten-thousandth of an inch (0.0001 in). They come in various styles – outside, inside, depth, and more – each with a specific purpose.
Safety Guidelines
Adhering to safety guidelines is a top priority for CNC operators since they work with potentially hazardous machinery. A few key safety protocols include:
- Personal Protective Equipment (PPE): Appropriate PPE such as safety goggles, ear protection, and steel-toed footwear should be worn at all times.
- Machine Guards: CNC machines often come with safety guards to protect operators from flying chips and debris. These guards should be checked and maintained regularly.
- Emergency Stops: Familiarize yourself with the location of emergency stops on machines and be prepared to use them in case of a malfunction or emergency.
Maintenance and Cleaning
Routine maintenance and cleaning of CNC machines and tools are critical to the operator’s responsibilities. A well-maintained machine runs more efficiently and accurately while reducing the risk of accidents. Among the maintenance tasks, CNC operators should frequently check:
- Toolholders and cutting tools: Regular inspection and proper storage prevent damage to these critical components.
- Lubrication: All moving machine components require lubrication to reduce wear and friction, ensuring smooth operation.
- Coolant: Proper coolant levels and clean filters help maintain the accuracy and lifespan of both the CNC machine and the cutting tools.
In summary, a CNC operator uses a variety of tools and equipment, such as calipers and micrometers, to ensure accuracy and quality in machined parts production. Additionally, they must prioritize safety and follow established guidelines while also conducting regular machine maintenance and cleaning.
Industries and Work Environments
Manufacturing Industry
A CNC operator plays a crucial role in the manufacturing industry, programming and operating computer numerical control (CNC) machines to produce specific parts and components. These operators ensure the equipment runs smoothly, maintain it to minimize downtime, and produce accurate parts based on provided blueprints. The work environment in manufacturing facilities is often noisy and hot, and CNC operators may encounter flying pieces of metal or parts. Physical demands in manufacturing include:
- Standing for long periods of time
- Bending, reaching, lifting, carrying up to 75 pounds
- Working with machine tooling equipment
Aerospace
CNC operators are essential in the aerospace industry, where precision and accuracy are mandatory. They create components for aircraft and spacecraft, ensuring the parts meet strict aerospace standards. CNC operators in this field work closely with engineers and other professionals to manufacture durable, lightweight pieces that can withstand extreme conditions.
Metalworking
In the metalworking industry, CNC operators work with a variety of metals to create parts and components for various applications. They must have a solid understanding of different metal properties and be able to adapt their machine settings accordingly. The metalworking environment can be challenging, as exposure to metal dust and debris may occur. Proper safety measures like protective eyewear and clothing are essential for CNC operators in this field.
Metal Fabrication
CNC operators in the metal fabrication industry play a vital role in creating custom-made metal products, such as structural components, industrial machinery, and decorative pieces. With their expertise in CNC machines, these operators can create intricate parts and components that would be difficult or impossible to produce through manual processes. In metal fabrication, CNC operators need to have good organizational skills and be able to work efficiently on projects with tight deadlines.
Career Path and Advancement
CNC Machinist and Programmer
CNC operators, also known as machinists, work with computer numerical control (CNC) machines to create and produce precision parts for various industries. They often start their careers by earning a degree or completing a vocational program in machining or a related field. Some machinists may also learn the trade through an apprenticeship or on-the-job training. As they gain experience and develop their skills, CNC machinists can advance to become CNC programmers.
CNC programmers are responsible for writing the code that controls the CNC machines. They use computer-aided design (CAD) and computer-aided manufacturing (CAM) software to create and test the programs, ensuring that the machines produce the desired parts accurately and efficiently. To become a CNC programmer, an individual typically needs a strong background in mathematics, knowledge of CAD/CAM software, and experience working as a CNC machinist.
Management Positions
As CNC machinists and programmers gain experience and expertise in their roles, they may have opportunities to move into management positions. Management roles in the CNC field can include supervisory positions, such as a production supervisor or team leader, where they oversee the work of other machinists and programmers, ensuring productivity and quality standards are met. Other management positions may involve operations or plant management, where individuals are responsible for overseeing the entire production process and implementing strategies to improve efficiency and reduce costs. To successfully transition into a management role, it is important for CNC professionals to develop strong leadership, communication, and problem-solving skills.
Specialized Industries
CNC operators can also advance their careers by specializing in specific industries or types of machinery. Some of the specialized industries that employ CNC machinists and programmers include aerospace, automotive, medical device manufacturing, and mold making. These industries typically use more advanced machines, usually 5 axis cnc machines. By focusing on a particular industry, CNC professionals can develop expertise in the unique requirements and intricacies of that field, increasing their value and opportunities for advancement.
In summary, the career path for CNC operators involves starting as a machinist and potentially advancing to a CNC programmer or a management role. Whether specializing in specific industries or taking on leadership positions, there are numerous opportunities for CNC professionals to grow and develop throughout their careers.
Job Outlook and Salaries
Entry-Level Positions
Entry-level CNC operators typically begin their careers with a basic understanding of computer numerically controlled (CNC) machines. They often gain experience through on-the-job training or postsecondary education. Entry-level CNC positions typically pay less than experienced positions, with a median annual wage of around $38,040 for metal and plastic machine workers 1.
Experienced CNC Operators
As CNC operators gain experience and develop their skills, their salaries tend to increase. The average hourly wage for a CNC operator in the United States is $20.33, while more specialized positions such as CNC lathe operators earn an average of $22.70 per hour2. CNC machinists, who usually have more experience and expertise, earn an average of $24.58 per hour2.
Benefits and Perks
In addition to competitive salaries, CNC operators may also enjoy various benefits and perks, depending on the employer. These may include:
- Health insurance
- Retirement plans
- Paid time off
- Overtime pay
- Performance bonuses
- Training and development opportunities
Financial benefits aside, CNC operators often find satisfaction in their work, contributing to the manufacturing industry’s growth and innovation.
Footnotes
- U.S. Bureau of Labor Statistics, Occupational Outlook Handbook, Metal and Plastic Machine Workers, https://www.bls.gov/ooh/production/metal-and-plastic-machine-workers.htm ↩
- Indeed, CNC Operator Salary in United States, https://www.indeed.com/career/cnc-operator/salaries/US ↩ ↩2