Canned cycles are an essential part of CNC machining, allowing for the automation of repetitive machining operations. In simple terms, canned cycles are a series of pre-programmed instructions that tell a CNC machine how to perform a specific machining task, such as drilling, boring, or threading. By using canned cycles, operators can save time and reduce the risk of errors, as they do not need to program every individual movement of the machine.
Canned cycles are usually modal, which means that they remain active until the canned cycle cancel command is executed. This makes them particularly useful for repetitive tasks, as the operator only needs to program the canned cycle once, and the machine will continue to perform the task until instructed otherwise.
What Are Canned Cycles?
Canned cycles are written in G-code, which is the language used to control CNC machines. G-code is a set of programming instructions that tell the machine what to do. Canned cycles are a type of G-code that simplifies the programming process by providing a set of pre-defined instructions.
They are called “canned” because they provide a concise and easy way to program a machine to produce a feature of a part.
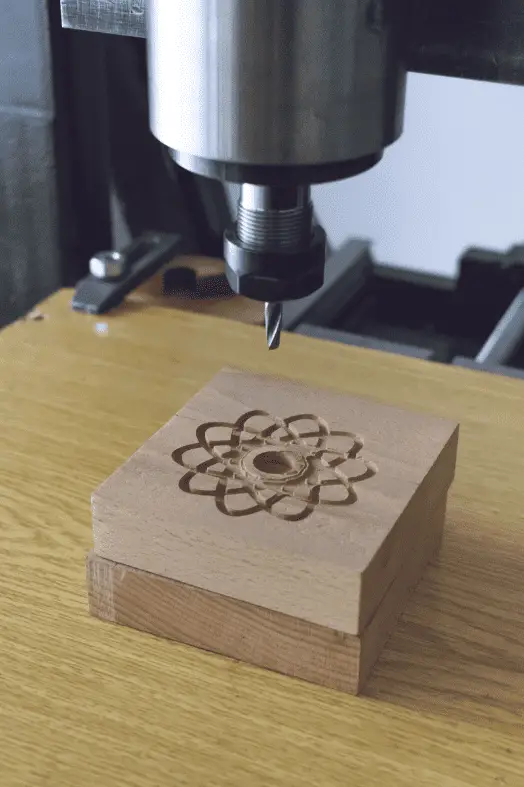
Canned cycles can be created and stored in a CNC machine’s memory, or they can be created using CAD/CAM software and then transferred to the machine. They can also be used in conjunction with manual programming to create more complex machining operations.
Canned cycles can be further customized by setting parameters such as feed rate, spindle speed, and depth of cut. This allows the operator to fine-tune the machining process to achieve the desired results.
Canned cycles are a powerful tool that simplifies CNC programming and improves machining efficiency. By automating repetitive tasks and reducing the likelihood of errors, canned cycles save time and improve the quality of machined parts.
Types of Canned Cycles
In this section, we will discuss the different types of canned cycles that are commonly used in CNC machining.
Drilling Cycles
Drilling cycles are used to drill holes in a part. The standard drilling cycle is the most basic canned cycle and is used for drilling simple holes. The G81 command is used to activate the standard drilling cycle. The cycle includes rapid movement to the drilling position, drilling to the specified depth, and rapid retraction of the drill bit.
Peck drilling cycles, such as G73 and G83, are used for drilling deep holes. These cycles allow the drill bit to retract periodically during the drilling process to clear chips and prevent the drill bit from breaking. G73 is used for high-speed peck drilling, while G83 is used for precision peck drilling.
Boring Cycles
Boring cycles are used to enlarge existing holes in a part. The G87 command is used to activate a boring cycle. The cycle includes rapid movement to the boring position, boring to the specified depth, and rapid retraction of the boring tool.
Tapping Cycles
Tapping cycles are used to cut threads in a hole. The G84 command is used to activate the tapping cycle. The cycle includes rapid movement to the tapping position, tapping to the specified depth, and rapid retraction of the tap.
The G74 command is used for the left-hand tapping cycle, while the G84 command is used for the right-hand tapping cycle.
How Canned Cycles Work
Canned cycles work by using G-Code commands that take repetitive machine movements that the CNC program can use. Operators do not need to program every motion of the machine. Instead, canned cycles allow for a concise way to program a machine to produce a feature of a part. The codes for canned cycles are within the larger program, which is a code within a code.
Canned cycles can include various parameters such as R, Z, P, I, peck, dwell time, spindle speed, feed rate, XY coordinates, incremental positioning, shift amount, retract plane, tool retract, and spot drill. These parameters can be adjusted as needed to achieve the desired results.
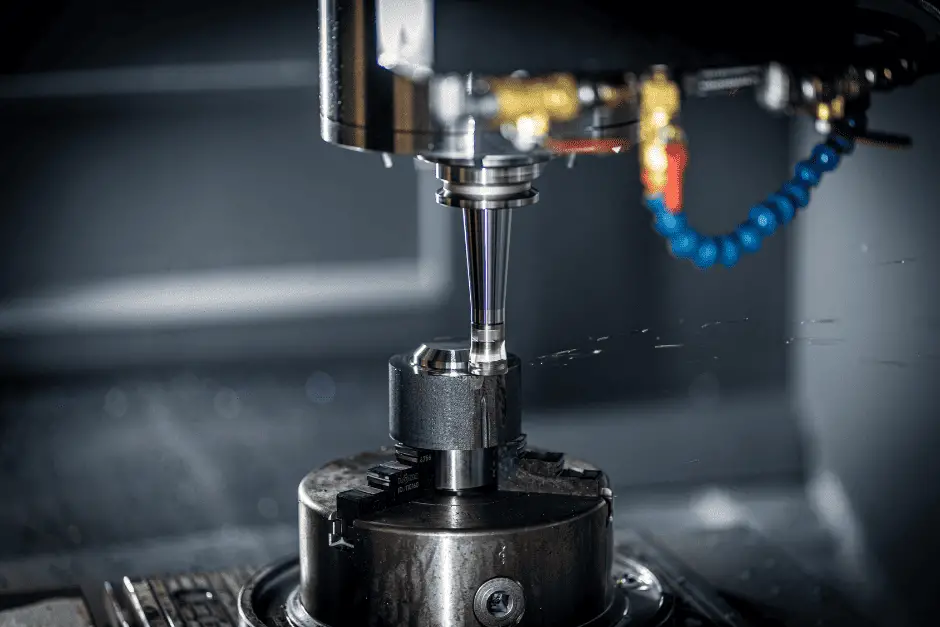
For example, the G81 canned cycle is used for drilling. The operator will need to specify the XY coordinates of the hole and the Z depth of the hole. The R parameter is used to specify the size of the hole, and the peck parameter is used to control the depth of each drilling pass. The dwell time parameter is used to pause the drill at the bottom of the hole to allow the chips to clear.
Another example is the G83 canned cycle, which is used for peck drilling. It is similar to the G81 canned cycle but adds the peck parameter to control the depth of each drilling pass. The retract parameter is used to specify the distance the drill bit retracts between each peck.
Advantages of Using Canned Cycles
Canned cycles offer several advantages over manually programming CNC machines. Here are some of the benefits of using canned cycles in CNC machining:
Efficiency
Canned cycles automate certain machining functions, such as drilling, boring, threading, pocketing, and more. Repetitive operations, such as drilling, tapping, and boring, use canned cycle codes. This automation saves time and increases productivity. By using canned cycles, CNC programmers can reduce the amount of time and effort required to program a machine to produce a feature of a part.
Consistency
Canned cycles repeat the same motions every time they are executed. This consistency ensures that the same machining process is performed on every part, resulting in consistent quality. Canned cycles also reduce the chances of human error, which can occur when manually programming a machine.
Quality
Canned cycles provide greater control over tool feed and depth of cut, which helps to improve the quality of the finished product. By varying the depth of cut by just changing one parameter, CNC programmers can achieve greater precision and accuracy in their machining operations.
Accuracy
Canned cycles provide greater accuracy in machining operations. By automating certain machining functions, canned cycles reduce the chances of errors that can occur when manually programming a machine. This results in greater accuracy and precision in the finished product.
Tool Life
Canned cycles help to extend the life of cutting tools. By providing greater control over tool feed and depth of cut, canned cycles reduce the wear and tear on cutting tools. This results in longer tool life and lower tooling costs.
Safety
Canned cycles help to improve safety in machining operations. By automating certain machining functions, canned cycles reduce the chances of accidents that can occur when manually programming a machine. This results in a safer working environment for operators and other personnel involved in the machining process.
Overall, canned cycles offer several advantages over manually programming CNC machines. By automating certain machining functions, canned cycles save time, increase productivity, improve quality, accuracy, tool life, and safety.
Applications of Canned Cycles
Canned cycles are widely used in CNC machining to automate repetitive tasks and simplify programming. They are available for a variety of machining operations, including milling, turning, threading, and deep hole drilling. In this section, we will discuss some common applications of canned cycles.
Milling
Canned cycles are commonly used in CNC milling machines to perform operations such as drilling, boring, pocketing, and facing. For example, a drilling canned cycle can be used to drill a series of holes with a specific depth and spacing. Similarly, a pocketing canned cycle can be used to remove material from a workpiece to create a pocket of a specific size and shape.
Turning
Canned cycles are also used in CNC turning machines to perform operations such as facing, turning, grooving, and threading. For example, a turning canned cycle can be used to turn a workpiece to a specific diameter, while a threading canned cycle can be used to cut threads of a specific size and pitch.
Deep Holes
Canned cycles are particularly useful for deep hole drilling, which involves drilling a hole with a depth-to-diameter ratio of more than 10:1. Deep hole drilling canned cycles can automate the process of peck drilling, which involves drilling a hole in small increments to prevent chip buildup and improve chip evacuation.
Fanuc Control
Canned cycles are supported by many CNC controllers, including the popular Fanuc control. Fanuc controllers have a range of canned cycles for milling, turning, drilling, and tapping operations. These canned cycles can be customized to suit specific machining requirements.
Conclusion
Canned cycles are an essential part of CNC machining. They automate repetitive machine movements and simplify the CNC program by using a single block with a G-code to specify the machining operations usually specified in several blocks. As a result, they allow for shorter code in the CNC programs, making it easier for operators to program the machine.
One of the most significant benefits of canned cycles is that they reduce the amount of time required to program the machine. This is because canned cycles automate certain machining functions such as drilling, boring, threading, pocketing, etc. This allows operators to focus on other aspects of the machining process, such as setting up the machine and monitoring its progress.
Canned cycles also improve the accuracy of the machining process. For example, the G83 cycle allows for dwells at the bottom of the hole, which increases the accuracy of the hole depth. Similarly, the G76 cycle allows for threading operations, which are accurate and precise due to their canned nature.
In addition, canned cycles can be customized to suit specific machining requirements. For example, the G89 cycle is a counterboring cycle that can be customized to specify the depth and diameter of the counterbore.
Finally, it is important to note that canned cycles require a coolant to be used during the machining process. This is because the canned cycle is designed to remove a large amount of material quickly, which generates a lot of heat. The coolant helps to dissipate this heat and prevent damage to the cutting tool and the workpiece.
In conclusion, canned cycles are an essential part of CNC machining that can significantly improve the accuracy and efficiency of the machining process. By automating repetitive machine movements and simplifying the CNC program, canned cycles allow operators to focus on other aspects of the machining process, such as setting up the machine and monitoring its progress.
Frequently Asked Questions
What are some examples of canned cycles?
Canned cycles are pre-programmed sequences of machine operations that can be repeated multiple times without the need for manual input. Some examples of canned cycles include drilling cycles, milling cycles, tapping cycles, boring cycles, and pocket milling cycles.
How are canned cycles coded?
Canned cycles are coded using G-codes, which are standardized programming codes used to control CNC machines. Each canned cycle has a specific G-code associated with it. For example, the G81 code is used for drilling cycles, while the G83 code is used for peck drilling cycles.
What is a drilling canned cycle?
A drilling canned cycle is a pre-programmed sequence of machine operations used for drilling holes in a part. It includes commands for drilling, retracting, and positioning the tool. The G81 code is used for drilling canned cycles.
What is a milling canned cycle?
A milling canned cycle is a pre-programmed sequence of machine operations used for milling operations on a part. It includes commands for tool positioning, cutting, and retracting. The G73 code is used for peck drilling canned cycles.
How do you activate a canned cycle in a part program?
To activate a canned cycle in a part program, the appropriate G-code for the canned cycle must be included in the program. The G-code will specify the type of canned cycle to be used, as well as any necessary parameters, such as the depth of cut or the number of repetitions. Once the program is executed, the CNC machine will automatically perform the canned cycle.