Thread milling is a cutting process commonly used in cnc machining to produce both internal and external threads. This versatile technique employs a milling operation that involves the circular ramping movement of a rotating tool which creates the thread pitch. Depending on the application, thread milling can be a highly efficient alternative to traditional thread turning, providing increased productivity and precision.
In order to create high-quality threads through thread milling, a CNC machine capable of operating in three directions simultaneously is required. The CNC machine interpolates the milling tool’s movements, resulting in controlled shaping of the thread’s major diameter. Moreover, thread milling offers advantages in materials where taps may break and is well-suited for blind and through-hole applications.
An array of specialized thread milling tools are available in the market, catering to diverse workpiece specifications and industry demands. Companies such as Kennametal and Sandvik Coromant offer a variety of options, ensuring optimal performance and precision during the thread milling process.
Thread Mills and Materials
Workpiece Materials
Thread milling is an effective way to create internal and external threads in various workpiece materials. Thread mills are designed to handle a variety of materials such as:
- Low-carbon steels
- Medium-carbon steels
- High-carbon steels
- Stainless steels
- Aluminum alloys
- Titanium alloys
- Inconel
- Cast iron
- Hardened steels (depending on the thread mill type)
Thread Mills Types
There are several types of thread mills available to suit different applications and materials. Some common types are:
- Single Profile Thread Mills – These thread mills have a single thread profile, which follows the contours of the thread form. They can be used for a wide range of thread sizes and pitches.
- Full Profile Thread Mills – Full profile thread mills have cutting edges that go around the entire circumference of the tool, allowing them to machine the entire thread profile in one 360-degree helical movement. They are suitable for materials with more challenging thread milling properties, such as high-temperature and hardened materials. An example of this type is the SHUR-THREAD™ from Emuge Corporation.
- Vario-Z Thread Mills – These thread mills have an increased flute count and are designed to improve thread quality and reduce cycle times. They are ideal for milling deep threads in tough materials.
- Drill & Thread Mills – These combine drilling and thread milling, allowing them to drill a hole and create threads in one operation. An example of this type is the THRILLER from Emuge Corporation.
- Indexable Insert Thread Mills – These thread mills use replaceable carbide inserts enabling the milling of large diameter threads. An example of this type is the GIGANT-IC from Emuge Corporation.
Hardened Steels
Machining threads in hardened steels can be challenging. However, by choosing the right type of thread mill and proper cutting parameters, it is possible to achieve good results. Tips for thread milling in hardened steels include:
- Selecting a thread mill with a sufficient number of cutting edges to handle the material, as suggested by Modern Machine Shop.
- Using coated carbide thread mills can help enhance tool life and performance in hard materials.
- When milling external threads, maintain a smaller radial depth and a 90° entering angle for the nose radius.
It is essential to consider the material and application when choosing the right thread mill for the job. Thread mills offer versatility and adaptability, making them an excellent choice for the machining of a wide range of materials and threading applications.
Thread Milling Techniques and Operations
Helical Interpolation
Helical interpolation is a key technique in thread milling that involves the circular ramping movement of a rotating tool. This method allows for the accurate production of both internal and external threads. The lateral movement of the tool in one revolution generates the thread pitch, which can be precisely controlled using the machine’s cutter compensation. In this process, the tool follows a helical path to create the desired thread profile. This technique is particularly valuable for producing complex thread forms and for machining high-quality threads in hard materials.
Z-Axis Movement
Z-axis movement in thread milling is essential to ensure the precise formation of the thread. The Z-axis refers to the vertical axis of a CNC machine, and it is responsible for controlling the depth of cut during the thread milling process. Accurate Z-axis movement is critical in achieving the desired thread form, pitch, and depth. Proper coordination between the X, Y, and Z axes ensures efficient and accurate thread milling operations.
Multi-Tooth Milling
Multi-tooth milling is another important thread milling technique that involves synchronizing multiple cutting edges on a single tool. This approach offers several advantages, including:
- Increased productivity: Multi-tooth milling can produce threads more quickly than single-tooth milling, resulting in increased productivity and shorter cycle times.
- Better chip management: With several teeth engaged in the cut, the chip load per tooth is reduced, leading to improved chip evacuation and reduced risk of chip-related tool damage.
- Greater stability: The cutting forces are more evenly distributed across multiple teeth, which can help to reduce tool deflection and improve thread accuracy.
Overall, thread milling techniques such as helical interpolation, Z-axis movement, and multi-tooth milling enable the efficient and accurate production of high-quality threads in a variety of materials. By understanding and applying these techniques, manufacturers can maximize thread milling performance and achieve precise, consistent results.
Comparing Thread Milling Methods
Tapping vs Thread Milling
Tapping and thread milling are two common methods for creating threads in a workpiece. Tapping involves forming threads by forcing a tap into a pre-drilled hole, whereas thread milling uses a rotating cutting tool to create threads in a helical motion.
- Speed: Tapping is generally faster than thread milling, as it takes less time to form threads in a hole. However, thread milling offers more flexibility, as it can be used to create different thread sizes and types with a single cutting tool, source.
- Versatility: Thread milling is more versatile than tapping, as it can be used to create both internal and external threads in a wide range of materials. Tapping, on the other hand, is generally limited to creating internal threads.
- Tool Life: Thread milling tools typically have a longer tool life compared to taps due to less wear and breakage risks, as the cutting forces are distributed more evenly.
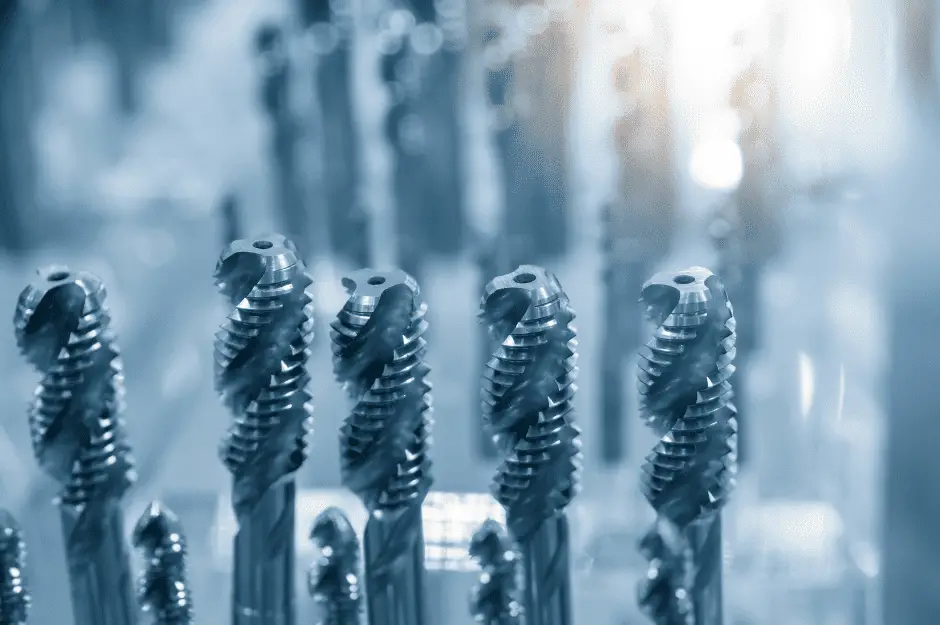
Turning vs Thread Milling
Turning is a machining process where a stationary cutting tool removes material from a spinning workpiece, while thread milling creates threads by moving a cutting tool along the desired thread profile.
- Thread Quality: Thread milling offers better thread quality, as the cutting tool can create a full thread profile in fewer passes compared to turning, source.
- Material Compatibility: Thread milling is more suitable for materials that are difficult to machine, such as hard, brittle, or high-temperature resistant materials. Turning may not provide satisfactory results in such materials.
- Setup: Turning typically requires less setup time compared to thread milling, as it does not need special programming or toolpath generation.
Drilling vs Thread Milling
Drilling is a machining process that removes material by using a rotating cutting tool to create a hole, while thread milling creates threads using a cutting tool’s helical motion within a pre-existing hole.
- Hole Depth: Thread milling has an advantage in creating deep threads, as it can produce threads in holes with larger depth-to-diameter ratios compared to drilling, source.
- Accuracy: Thread milling offers higher dimensional accuracy and better thread quality compared to drilling. It also allows for the adjustment of the thread form by altering tool movement.
- Burrs: Drilling often results in burrs, which need to be removed after machining. Thread milling, on the other hand, typically does not produce burrs, so no additional deburring is required.
In conclusion, the choice between tapping, turning, drilling, and thread milling depends on factors such as speed, versatility, material compatibility, and the desired thread quality. Each method has its advantages and disadvantages, so it’s crucial to consider the specific requirements of the application when selecting the appropriate method.
Programming and CNC Machines
Program
Thread milling is a process that involves the use of a CNC milling machine to create internal and external threads. When it comes to programming a thread milling operation, two important numbers must be considered: the thread pitch and the pitch diameter offset.
The program used in CNC machines requires a specific G-code that tells the machine how to cut the threads. This code is essential in providing precise and accurate results. The program needs to account for tool selection, spindle speed, feed rate, and other vital settings for thread milling.
S Code
The S code is used to define the spindle speed during a thread milling operation. It’s essential to select the appropriate spindle speed based on material type, tool material, and desired thread finish. The S code can be calculated using formulas and guidelines provided by the tool or machine manufacturer. Proper spindle speed is necessary for minimizing tool wear, avoiding chatter, and achieving the desired thread profile with high accuracy.
Here’s an example of a simple G-code for a thread milling program:
N2 G20
N4 G80 G40 G17
N6 T1 M6
N8 G90 G54 S2204 M3
N10 G00 X0. Y0. M8
N12 G43 Z0.1 H1
N14 G90 G00 Z-0.5
N16 G91 G00 X0.0185 Y0.0013
N18 G01 G41 X0.0623 Y0.0045 F4.76 D1
N20 G03 X-0.0858 Y0.114 Z0.0192 I-0.0982 J0.0154
N22 G03 X0. Y0. Z0.0769 I0.0051 J-0.1199
N24 G03 X-0.0759 Y-0.1209 Z0.0192 I0.0206 J-0.0972
N26 G01 G40 X0.0625 Y0.0007
N28 G00 X0.0185 Y0.0002
N30 G00 G90 Z0.1
N32 G91 G28 Z0.
N34 M30
Programming a CNC machine for thread milling requires careful planning and accurate execution of the program to produce high-quality threads. It’s essential to consider factors such as spindle speed, tool selection, and pitch diameter offset to ensure the milling machine performs the correct sequence of operations for successful thread milling.
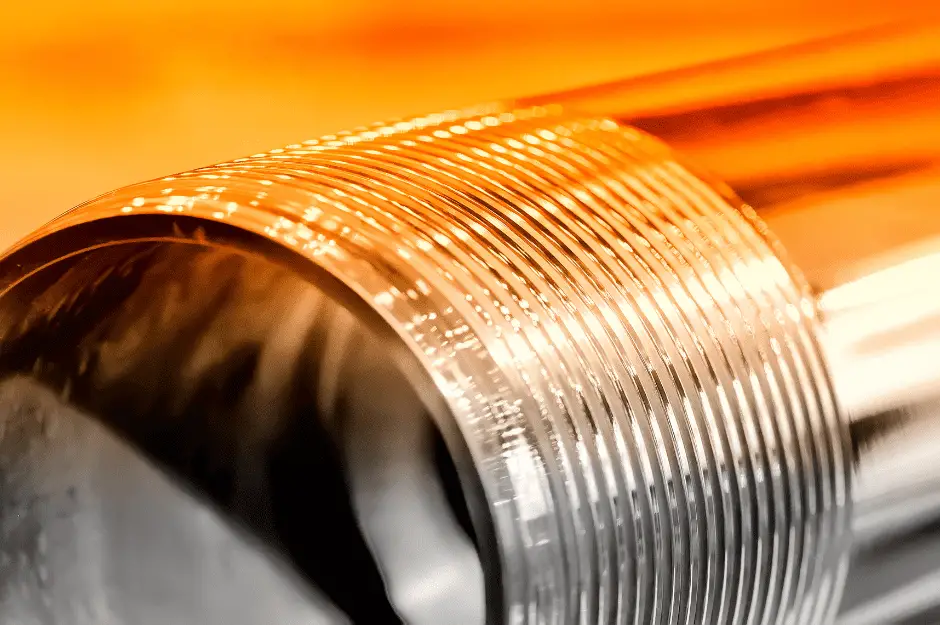
Thread Milling for Pipe Threads
Thread milling is a machining process that involves using a cutter with a specific profile to create threads on the internal and/or external surface of a pipe. This section focuses on milling for pipe threads, which are essential for connecting pipes, fittings, and valves in various industries. The common types of pipe threads include NPT, NPTF, and BSPT.
NPT (National Pipe Taper)
NPT is a common threading profile used in the United States for sealing and connecting pipe fittings. It is a tapered thread that creates a tight seal when the male and female components are tightened together. The taper angle of NPT threads is 1°47′, which allows for easy engagement and tight connections. Thread milling for NPT threads requires a cutter that matches the specific taper angle and pitch to ensure proper thread engagement.
NPTF (National Pipe Taper Fuel)
NPTF is very similar to NPT in shape and dimensions but has a slightly different thread profile. The primary difference is that NPTF is designed to seal without the use of sealing compounds, such as tape or thread sealant, due to a more precise fit between threads. Milling NPTF threads can be done using similar tooling as NPT threads, but with a higher degree of accuracy and precision required.
BSPT (British Standard Pipe Taper)
BSPT is a common threading profile used in the United Kingdom and other countries, which follow British standards. This type of threading is also tapered, like NPT and NPTF, with a taper angle of 1°47′ and a rounded tip at the base of each thread, which assists in sealing the connection. To mill BSPT threads, a specific cutter with the appropriate profile, taper angle, and thread form is needed.
To achieve successful thread milling for pipe threads, such as NPT, NPTF, and BSPT, selecting the appropriate cutter and following proper machining techniques are crucial. Some essential considerations include using cutting tools made from high-quality materials, ensuring proper thread engagement, and setting the correct milling parameters. Additionally, using machines capable of simultaneous movements on the X, Y, and Z axes will provide accurate and efficient results in thread milling pipe threads.
Common Thread Milling Operations
Thread milling is a cutting process used to produce threads with a milling operation. CNC milling machines with three simultaneous axes are very popular and can be found in every small workshop, allowing for precise thread milling operations. This section will cover two common thread milling operations: Chamfering and Countersinking.
Chamfering
Chamfering is an essential step in thread milling, as it prepares the workpiece for threading by creating a beveled edge at the beginning of the thread. This process reduces the chances of tool breakage and eases the entry of subsequent cutting operations. A chamfering tool, also known as a deburring tool, is typically used to create the bevel.
When using thread mills for chamfering, it is important to consider the following factors:
- The chamfer angle, which is typically between 30° and 45°, depending on the specific application.
- The depth of the chamfer, which should be calculated based on the thread type and size.
- The cutting speed and feed rate, which vary depending on the workpiece material and tool type.
Countersinking
Countersinking is another important thread milling operation that is often used to create a conical recess at the top of a threaded hole, allowing for a flush fit of a countersunk screw head. This operation is particularly useful when working with materials that would otherwise be prone to cracking or deformation due to the pressure exerted by the screw head.
When executing countersinking in thread milling, be mindful of the following:
- The countersink angle, which is typically 82°, 90°, or 100°, based on the type of screw being used.
- The depth of the countersink, which should be sufficient to accommodate the screw head without compromising the strength of the workpiece.
- The cutting speed and feed rate, which are determined by factors such as the workpiece material and tool type.
By adhering to these guidelines, you can effectively perform common thread milling operations like chamfering and countersinking, ensuring a high-quality finish and efficient machining process. Remember to adjust the relevant parameters based on the specific requirements of your application and always use appropriate tooling to achieve the desired results.
Advantages of Thread Milling
Thread milling is an advanced machining process that allows craftsmen to create threads with high precision and efficiency. One of the significant advantages of thread milling is its ability to provide secure machining operations. This results from the minimal cutting forces and the generation of small chips, reducing the risk of machining stops and damage to the workpiece.
Another benefit of thread milling is its effectiveness in producing threads on difficult-to-machine materials. The excellent cutting conditions associated with thread milling make it possible to create threads on materials, such as hardened steel and titanium, that may pose challenges when using other threading methods.
Thread milling is known for its ability to produce threads with higher thread quality compared to other methods such as tapping. This is because thread milling offers better control over the cutting process, resulting in increased accuracy and consistency of the final product.
In addition, thread milling allows for multiple radial passes during the milling operation, which results in good chip control. Furthermore, the thread milling process can be performed on machines capable of moving on the X, Y, and Z-axis simultaneously, providing versatility to the machinist.
Carbide thread mills are a popular choice in the industry, and they offer several benefits, such as longer tool life. This extended tool life often comes with similar cycle times as tapped holes, making thread milling an efficient option for producing threads on a wide range of materials.
To summarize, thread milling offers several advantages, including secure machining operations, effectiveness on difficult-to-machine materials, higher thread quality, good chip control, and longer tool life for carbide tools. These benefits make thread milling an essential technique for machinists seeking high-quality and efficient thread production.
Visual Resources and Tutorials
When learning about thread milling, there are several visual resources and tutorials available to help better understand the process. One informative video produced by Vectric V11 provides a detailed overview of the thread milling toolpath strategy, examining the various options and their effects.
Another valuable resource is a tutorial from Bantam Tools that focuses on thread milling strategies using Fusion 360 software. This video features the Bantam Tools Desktop CNC Milling Machine milling threads in aluminum 6061, offering insights into programming a thread milling operation and important numbers such as thread pitch and pitch diameter offset.
For those looking for more in-depth technical information about thread milling, a comprehensive PDF guide created by Allied Machine covers topics such as hand-specific milling and Z-axis movement to produce the thread’s helix. This guide is helpful for understanding both right and left-handed thread milling applications.
A concise explanation and practical tips on thread milling can be found in an article from Modern Machine Shop. Here, the author uses a Sandvik Coromant-produced video to discuss the advantages of thread milling, application techniques, and how to program thread milling tool paths.
Incorporating a variety of visual resources and tutorials is essential for anyone looking to learn more about thread milling, as these materials offer practical insights and expert guidance on how to achieve the best results. Participants are encouraged to further explore these resources and combine them with hands-on experience to master the technique.