Trochoidal Milling
Trochoidal milling is a specialized cnc machining method used to create slots that are wider than the cutting tool’s diameter. By employing a series of circular cuts, known as a trochoidal tool path, this technique provides an efficient approach for machining tight spaces where chip clearance might be a concern. As a form of High Efficiency Milling (HEM), trochoidal milling achieves exceptional results through high-speed operations while maintaining a low radial depth of cut (RDOC) and a high axial depth of cut (ADOC) source.
In comparison to traditional milling methods, trochoidal milling reduces the challenges associated with evacuating thick, heavy chips from deep pockets and intricate features. This ensures that chips are less likely to be re-cut as the tool moves within the workpiece, improving surface quality and overall efficiency. When applied effectively, it provides a more secure process and improves tool life, leading to reduced tooling costs. source.
Fundamentals of Trochoidal Milling
Trochoidal Milling Process
Trochoidal milling is a method of cnc machining that uses a series of circular cuts, known as a trochoidal tool path, to create a slot wider than the cutting tool’s diameter. This technique is primarily used for roughing and semi-roughing of difficult materials such as hard steels, ISO H, and HRSA-materials, and ISO S. It can also be applied to other materials, especially in vibration-sensitive applications.
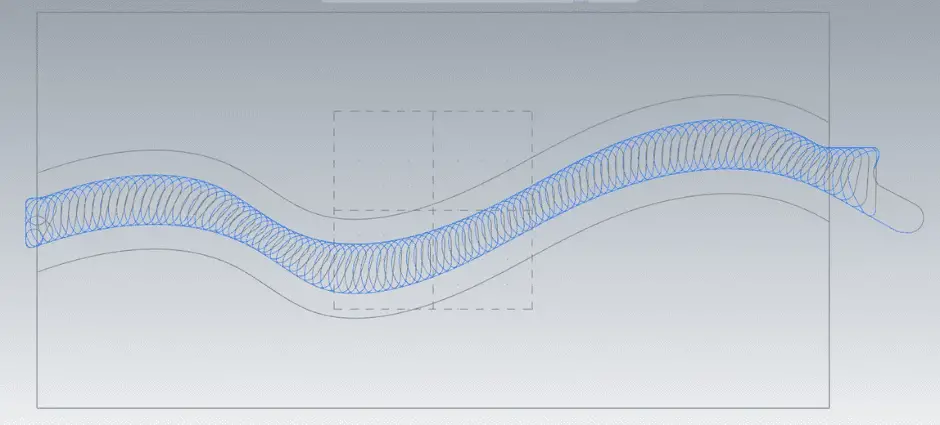
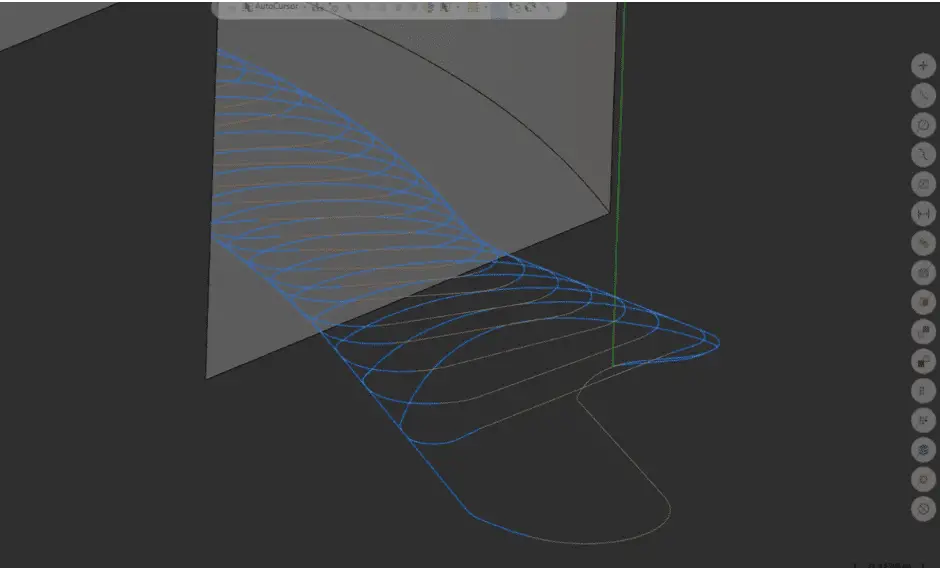
Playing the video above at 2X speed will give you a good representation of how fast this type of toolpath can run at.
High-Speed CNC Machining vs Conventional CNC Milling
There are key differences between high-speed machining (HSM) and conventional milling. HSM, which includes trochoidal milling, is characterized by:
- High cutting speeds
- High feed rates
- Low radial depth of cut
- High axial depth of cut
In contrast, conventional milling is characterized by:
- Lower cutting speeds
- Lower feed rates
- Larger radial depth of cut
- Smaller axial depth of cut
Trochoidal milling and other HSM techniques provide numerous benefits compared to conventional milling, such as:
- Improved productivity
- Increased tool life
- Better surface finish
- Less heat generation
- Reduced workpiece deformation
It’s important to note that HSM requires specific cutting tools that can withstand the high cutting speeds and feed rates. In many cases, it’s possible to use significantly higher cutting parameters when using trochoidal milling with dedicated end mills compared to conventional machining processes, which can shorten cnc machining times considerably.
In summary, trochoidal milling is a high-speed cnc machining process that enables faster material removal, improved surface quality, and longer tool life compared to conventional milling. It’s particularly useful for working with difficult materials and in vibration-sensitive applications.
Benefits of Trochoidal Milling
Extended Tool Life
Trochoidal milling’s unique circular tool path prolongs the tool life by distributing wear more evenly along its cutting edges. The technique consists of high speed, high axial depth of cut (ADOC), and low radial depth of cut (RDOC), ensuring that only minimal chip thickness is generated. This even wear minimizes tool wear, enabling tools to last longer and maintain peak performance.
Improved Material Removal Rates
Another advantage of trochoidal milling lies in its ability to improve material removal rates. Due to its high-speed movements, optimized cutting, and significantly reduced tool wear, trochoidal milling enables faster, more efficient material removal. This results in reduced machining times and increased productivity, ultimately benefiting the overall manufacturing process.
Reduced Cutting Forces and Vibration
The trochoidal milling technique is known for generating low radial cutting forces, which, in turn, place less demand on stability and enable a large depth of cut. Consequently, it reduces cutting forces and vibration during the milling process. This can lead to smoother, more accurate results, ultimately improving both roughing and finishing operations.
In conclusion, trochoidal milling offers a host of benefits, including extended tool life, improved material removal rates, and reduced cutting forces and vibration. This powerful milling technique can help optimize manufacturing operations and increase overall productivity.
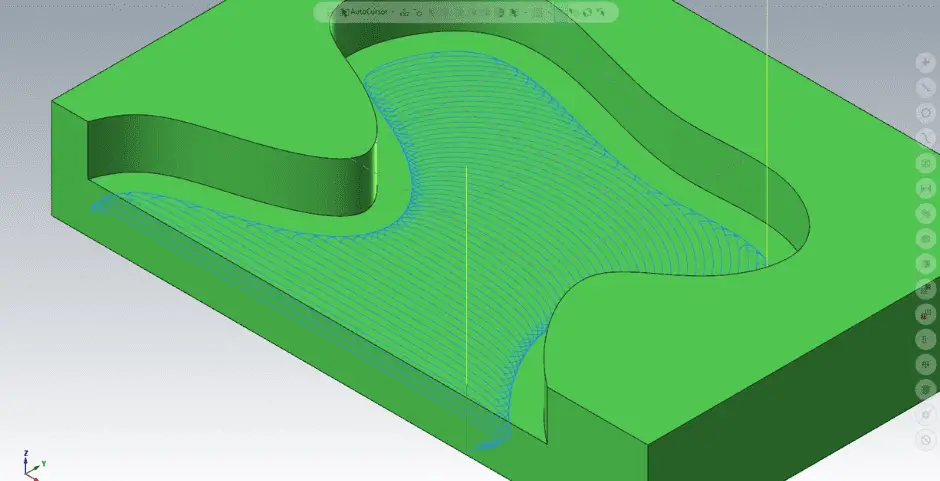
This video demonstrates the trochoidal tool path shown in the picture just above it.
Tools and Equipment
Cutting Tools and End Mills
In trochoidal milling, the selection of cutting tools and end mills is crucial for efficient operation. The cutting tools should have a small radial depth of cut along with a low axial depth of cut (Z-depth). This combination aids in producing a low radial cutting force, which places less strain on the cutting tool and the spindle. A solid carbide end mill with multiple flutes is usually preferred for trochoidal milling, as it provides excellent performance across a range of cutting conditions. Some appropriate high-speed machining (HSM) tools for trochoidal milling can be found in manufacturers such as Fraisa USA.
Spindle and RPM
The spindle plays an essential role in trochoidal milling, and its selection should be based on the cutting forces generated during the process. These forces are dependent on factors such as the cutter diameter, axial depth of cut, and feed rates. A strong and rigid spindle is necessary to maintain accuracy and control while conducting high-speed milling operations. Moreover, it is vital to select an appropriate RPM (rotations per minute) based on the cutting tool used and the material being machined to ensure optimal performance and tool life.
CAM Systems and Toolpath Generation
CAM (computer-aided manufacturing) systems are utilized to generate the toolpath for trochoidal milling. These software applications can produce dynamic milling toolpaths that maintain a low radial engagement, allowing for increased feed rates and reduced tool wear. Various CAM software packages, such as Mastercam, HSMworks, and Fusion 360, can be used for this purpose.
Trochoidal milling toolpaths are generated with a focus on maintaining constant tool engagement, ensuring that the cutting forces remain stable throughout the operation. This approach leads to efficient material removal, reduced vibration, and improved tool life. When generating the toolpath, it is essential to take into consideration factors such as cutter diameter, Z-depth, and engagement to optimize the process.
In conclusion, proper tool selection, spindle configuration, and CAM systems play a significant role in the success of trochoidal milling operations. By considering these factors, machinists can achieve efficient material removal, improved tool life, and reduced tool wear in their milling applications.
Application in Different Materials
Trochoidal milling is a versatile machining strategy that finds applications in different materials, owing to its ability to reduce heat and vibration during milling operations.
Machining Titanium and Stainless Steel
Trochoidal milling is particularly suitable for machining difficult materials like titanium and stainless steel. The method’s circular tool path and controlled feed rate allow for better chip evacuation, reduced cycle times, and improved tool life when compared to conventional milling techniques 1. In addition, trochoidal milling excels in applications like:
- Slotting
- Pocketing
- Roughing
For these materials, adjusting the radial depth of cut and stepover can lead to improved material removal rates (MRR) and minimized tool wear.
Micromachining and Hard Materials
Trochoidal milling is also an effective solution for micromachining and working with hard materials. Its ability to control chip thinning helps in reducing tool breakage. This method is especially beneficial for machining materials where chips are hard to break, like Inconel and other advanced alloys.
In hard machining applications, trochoidal milling reduces cycle times due to fewer tool changes and less time spent on tool carousel setup. Moreover, trochoidal milling allows for high-feed, high-speed cutting, optimizing MRR and enhancing overall process efficiency.
By carefully considering the material properties and machining requirements, trochoidal milling can be employed to optimize cutting performance across a wide range of applications and materials.
Trochoidal Milling Strategies
Trochoidal milling is a highly efficient and effective machining strategy that incorporates a small radial depth of cut, resulting in reduced cutting forces and improved tool life. This section covers four primary strategies used to optimize trochoidal milling: Roughing, Semi-Finishing and Finishing, Slot Milling and Pocketing, and Contour Milling and Air Blast.
Roughing
Roughing is the initial step in the trochoidal milling process, which focuses on removing large amounts of material quickly and efficiently. The primary aim is to maximize the material removal rate (MRR) while maintaining a consistent average chip thickness. By using small stepovers and high-feed cutting rates, roughing enables faster machining times and less stress on the cutting tool. This strategy is particularly beneficial for difficult-to-cut materials or large workpieces.
Semi-Finishing and Finishing
After the roughing phase, trochoidal milling moves on to semi-finishing and finishing operations. Semi-finishing focuses on refining the workpiece’s shape, while finishing aims to achieve the desired surface finish and dimensional accuracy. During these stages, smaller radial cuts and slower feed rates are employed to reduce cutting forces and ensure precise results. By carefully controlling the cutting parameters, it is possible to achieve a smooth and accurate surface finish while also prolonging tool life.
Slot Milling and Pocketing
Trochoidal milling is especially advantageous for slot milling and pocketing applications. The strategy involves using a combination of circular and transition curve movements to create slots and pockets with minimum material wastage. This type of milling technique can produce higher material removal rates while reducing the tool deflection and minimizing the heat generated during the machining process. By optimizing the cutting parameters, this method allows for efficient machining of deep slots and high flanks in a variety of materials.
In conclusion, trochoidal milling strategies help to optimize the machining process by reducing cutting forces, extending tool life, and improving part quality. By understanding and implementing the right strategies in roughing, semi-finishing, finishing, slot milling, pocketing, and contour milling, it is possible to achieve efficient and precise results in a wide range of applications.
Optimization Techniques
Parameters for Improved Productivity
Optimizing trochoidal milling parameters ensures higher productivity and efficient material removal. Key factors to consider include spindle speed (RPM), feed rate, and step-over. Stability Prediction and Step Optimization of Trochoidal Milling discusses the importance of selecting appropriate parameters to improve overall machining efficiency.
The tool engagement angle plays a significant role in the milling process, especially when machining tough materials. Using a low radial depth of cut allows for better stability and lower cutting forces while increasing the axial depth of cut, as shown in Slicing and Trochoidal Milling.
Effective Chip Evacuation Methods
Chip evacuation is crucial to maintaining the efficiency of the milling process. Effective chip removal methods can include:
- Air blast: Using air to clear chips from the cutting area allows for continuous machining without interrupting the process.
- Coolant flow: Ensuring proper coolant flow direction and pressure can aid in chip evacuation and reduce heat buildup.
Optimizing chip evacuation also contributes to reducing tool wear and improving overall machining times.
Reducing Tool Wear and Deflection
Tool wear and deflection are common issues in the milling process. Reducing them can help extend tool life and improve productivity. Some strategies for controlling wear and deflection include:
- Selecting the right tool material: Using a carbide endmill provides better resistance to wear and deflection.
- Optimizing toolpath generation: Following strategies like Bézier curve-based trochoidal tool path optimization can reduce stress on the tool and ensure more efficient material removal.
- Balancing tool engagement: Maintaining appropriate engagement angle and depth of cut promotes even tool wear and reduces deflection.
By incorporating these optimization techniques, operators can improve the efficiency and longevity of their trochoidal milling processes.