This article, just like my website, will concentrate on types of milling cutters that are used with hobby cnc machines. The amount of tooling available for industrial machines is mind boggling and way too much for one book, never mind one blog article. Threadmills are one example that is beyond the scope of a hobby cnc machine.
So, the main type of tools that cnc hobbyists use, and sometimes the only type they use, are end mills and ball end mills. Drills are used a lot if you work with metals, but this article will focus only on end mills and ball nose end mills.
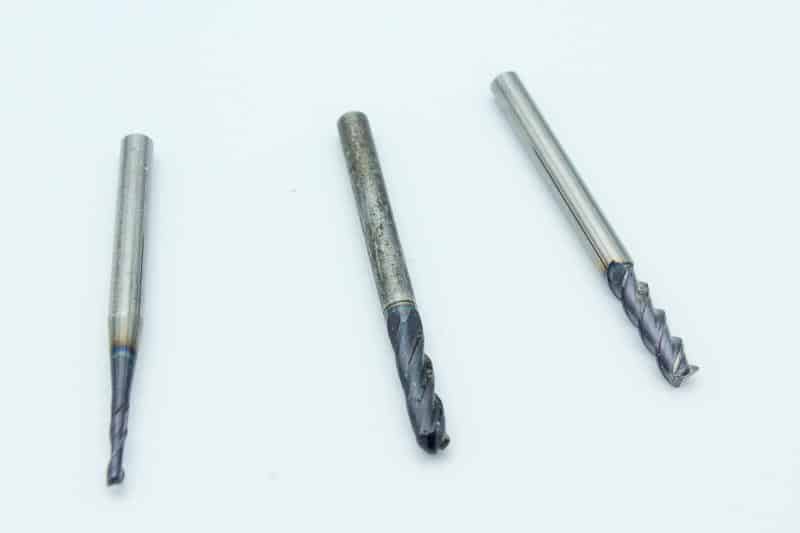
I have curated a list of common questions that people ask and have given an answer that best fits the concerns a cnc hobbyist may have.
End Mills
What is an end mill used for?
For an extremely basic answer, an end mill is rotated in the spindle of a milling machine and moved against a piece of material (metal or otherwise) and the rotating ‘blades’ on the edge of the tool will slice away material to produce the desired form or shape.
Originally an end mill was used to remove material using only the cutting flutes on the side of its diameter. So this would involve approaching the workpiece from the side, moving in the X and Y axes only to remove material with the side edge of the tool.
Fortunately the end mill evolved to include cutting edges on the bottom face vastly increasing its versatility into a workhorse tool that can accomplish most milling tasks.
Having cutting edges on the base of the tool enables it to plunge or ramp down into your material.
Combined with a cnc machine an end milling operation can be used to create slots, holes, contours and profiles to name only a few of the most common tasks.
The wide availability of carbide end mills, as opposed to high speed steel (less durable), increases its use to harder exotic materials or just to improve its life expectancy making the extra expense more cost effective, especially for a hobbyist.
If used properly and conservatively a carbide end mill can last quite a long time.
Can you drill with an end mill?
If it has cutting edges on the bottom face, yes, you can drill with an end mill.
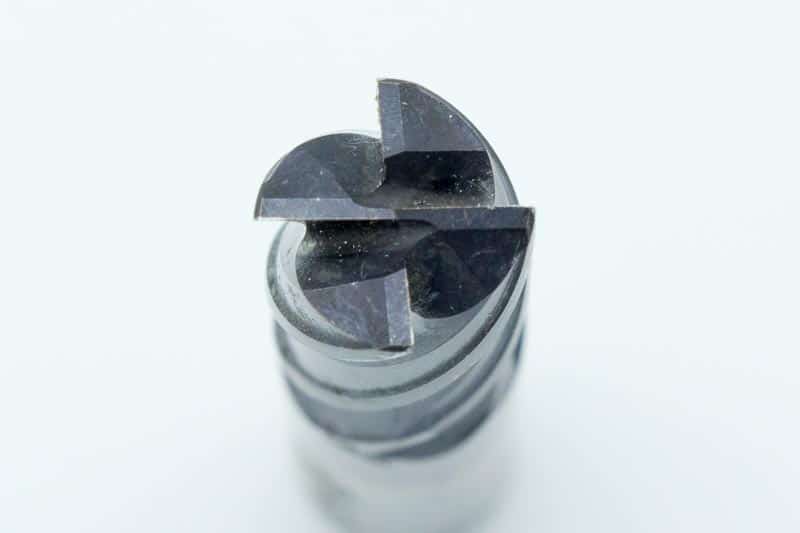
This is mainly described as ‘plunging’ and enables you to open up an ‘internal’ pocket without having to use another tool to open up a space for the end mill to move down into.
This ability does not replace the use of a drill bit and plunging a deep hole with an end mill is not good practice.
A deep hole can be milled with an end mill by using a smaller diameter tool than the required hole and cnc programming a ‘spiral’, ramping down in a circle. This is the better way to create a hole using an end mill with the added bonus of being able to fine tune and adjust the finished diameter.
What are 2 flute end mills for?
Two flute end mills are known as slot drills. They are primarily used for milling slots or pockets.
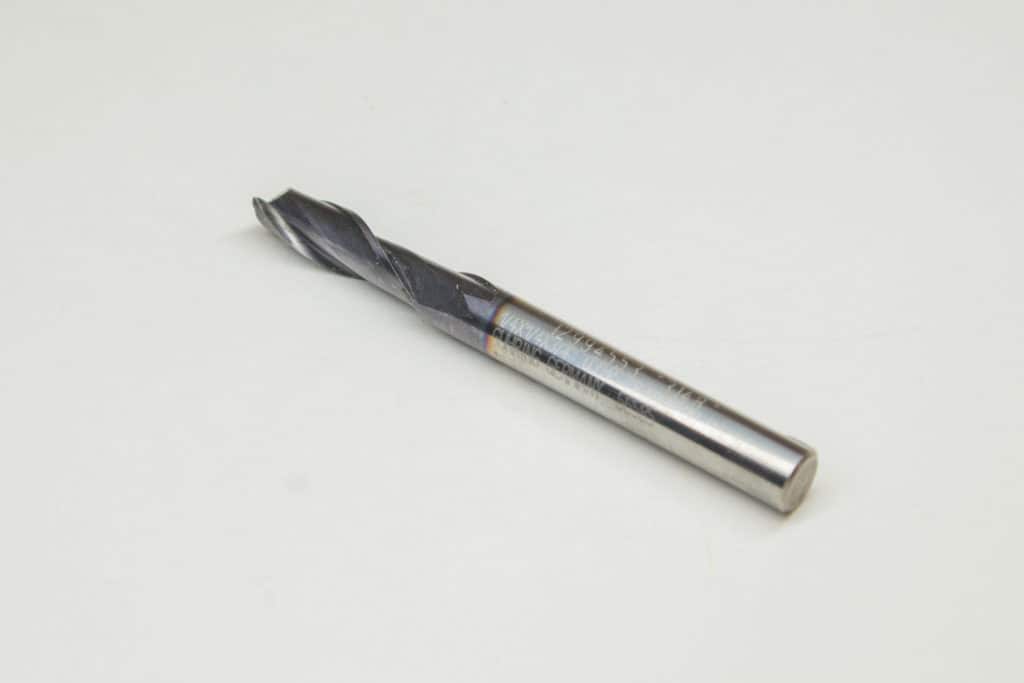
What is the difference between an end mill and a slot drill?
A slot drill is a two flute version of an end mill. They are specifically designed to plunge into material in the Z axis when milling a slot, e,g, for a keyway.
Having only two flutes increases the space in the spiral of the tool which gives more room for chips to evacuate.
This helps prevent the tool from clogging up and breaking when plunging.
This gives a slot drill the improved ability to plunge and mill a slot without breaking, hence the name.
Can an end mill plunge?
Most end mills have cutting edges on the bottom face which will let you plunge into your material.
Plunging is usually done at a slower feedrate than when milling along the X and Y axes and avoid going too deep before moving in X and/or Y directions. (shallow depth of cut).
A plunging feedrate of about 10% compared to your X and Y feedrate would be a good starting point.
What is an upcut end mill?
An upcut end mill is when the spiral of the side flute rakes backward. This will force the chips up and away from the workpiece helping to prevent a build up of chips and to prevent tool breakage.
Most end mills are designed as up cut.
The direction of the flute rake is the same as a drill bit which forces the chips along the flutes and out of the hole.
What is a down cut end mill?
A down cut end mill is when the spiral of the side flutes is raked forward. This forces the material being removed downward. These types of tools are primarily used on softer materials such as wood and plastic.
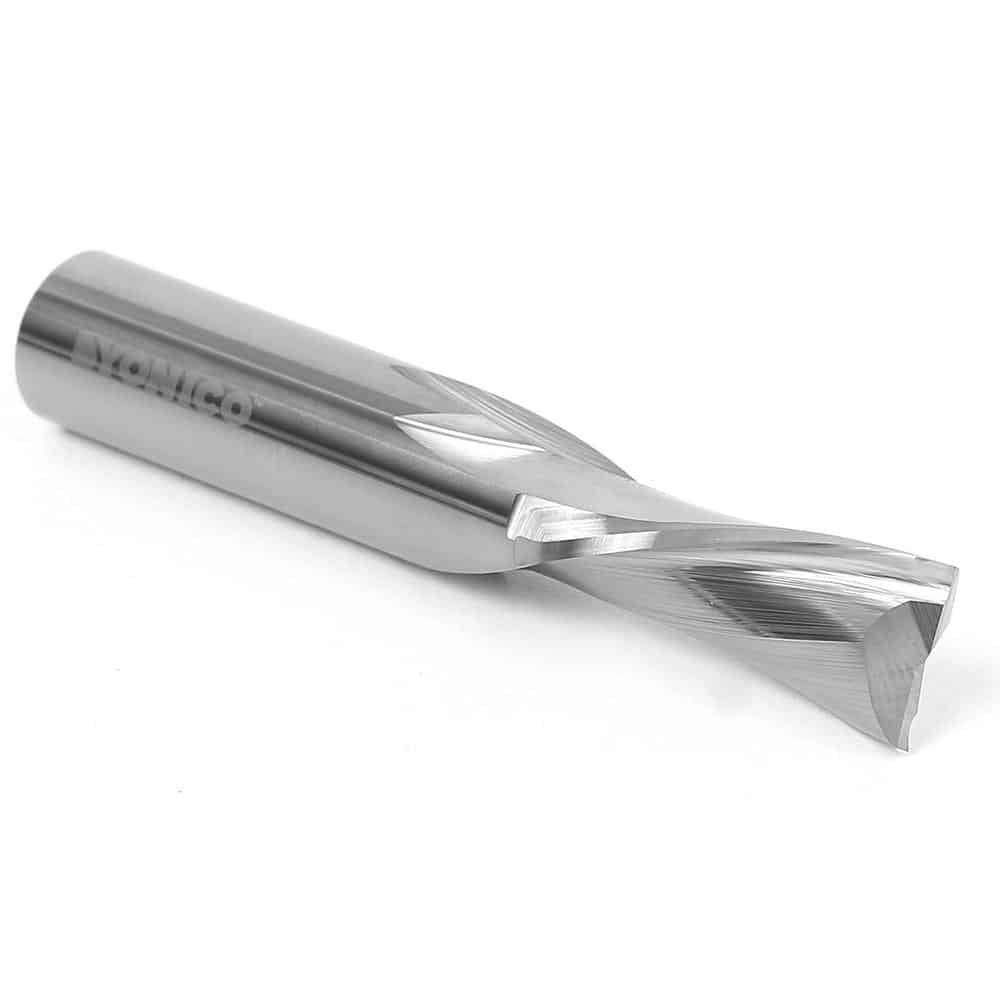
This design feature prevents the material splintering or chipping on the top edge improving the finish and appearance.
The tool is still designed to rotate in the same direction.
How can you tell if an endmill is center cut?
The cutting edges on the bottom face will extend all the way to the center.
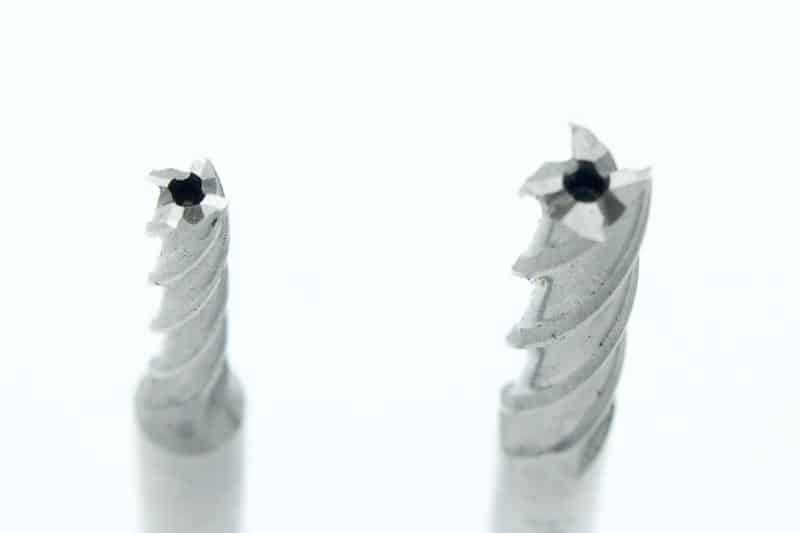
Some slot drills will have opposing flutes that meet slightly off center (asymmetrical). This helps the tool cut in the middle where the rotational speed is at its slowest.

How many flutes do you need for milling steel?
There is no specific requirement for a certain amount of flutes for milling steel. The amount of flutes can dictate what abilities the tool may have that make it better for specific operations.
For example, slot drills have two flutes and are designed for plunging.

An eight flute end mill will be able to feed faster using the same feed per tooth than a four flute end mill.
Is aluminum easier to mill than steel?
Yes, it’s a lot easier. Although trying to mill poor quality aluminum can be frustrating. The aluminum you can buy at the local big box store is not ideal for machining. It is typically gummy and clogs up and breaks end mills. It is too soft and only useful for fabrication etc.
Free machining Aluminum is what you want to buy, they typically have a grade such as 6061.
Sometimes these types of grades are referred to as aerospace grade or aircraft grade, which is just a fancy way of saying they are machinable.
What is the best endmill for aluminum?
There are end mills designed specifically for aluminum. They usually have a steep rake angle on the helix and have only two flutes. This is to take advantage of higher speeds and feeds that industrial machines can run at with aluminum, i.e. very fast.
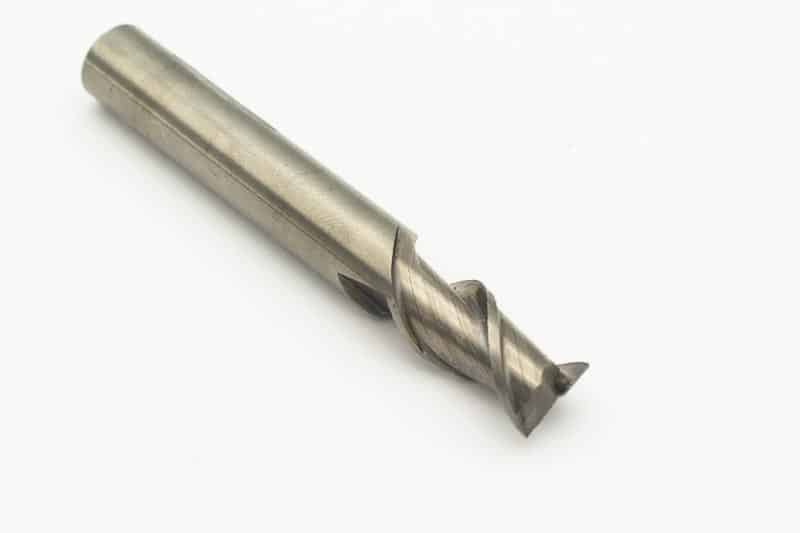
For hobby machines these high spindle speeds and feeds are not possible so just using an ordinary carbide end mill is fine and actually preferable.
Best endmill for stainless steel?
A good quality Carbide end mill will be the tool of choice for any hard alloys.
Just decrease the speeds and feeds to accommodate for the harder alloy and hope your hobby machine has the power to handle it.
Best end mill for wood?
Two flute and even one flute end mills, small dia ball end mills for finishing complex reliefs. There are also the burr style bits for machining wood. Upcut and downcut styles to suit different densities of wood etc.
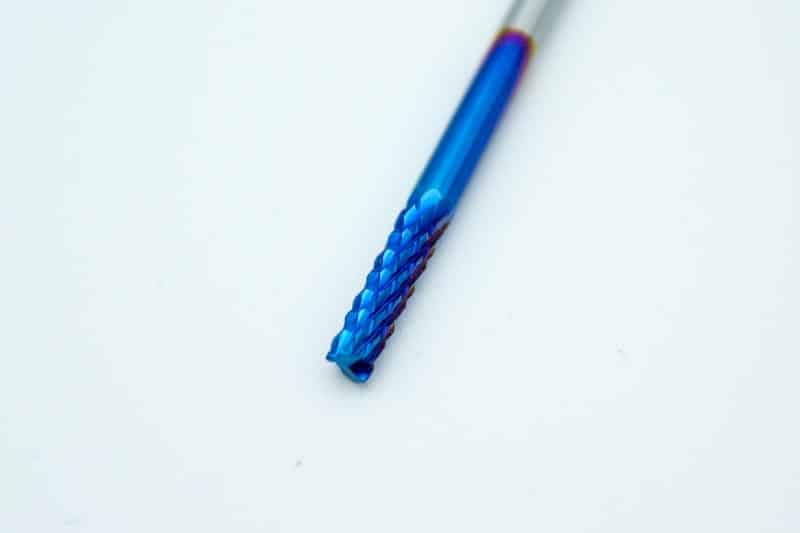
Wood is quite forgiving to machine, so test different styles and find what suits your needs.
Best end mill for plastic?
Single flute end mills are the best for cutting acrylic. This enables the machine to run at a high rpm yet still maintain an achievable feedrate for the required feed per tooth.
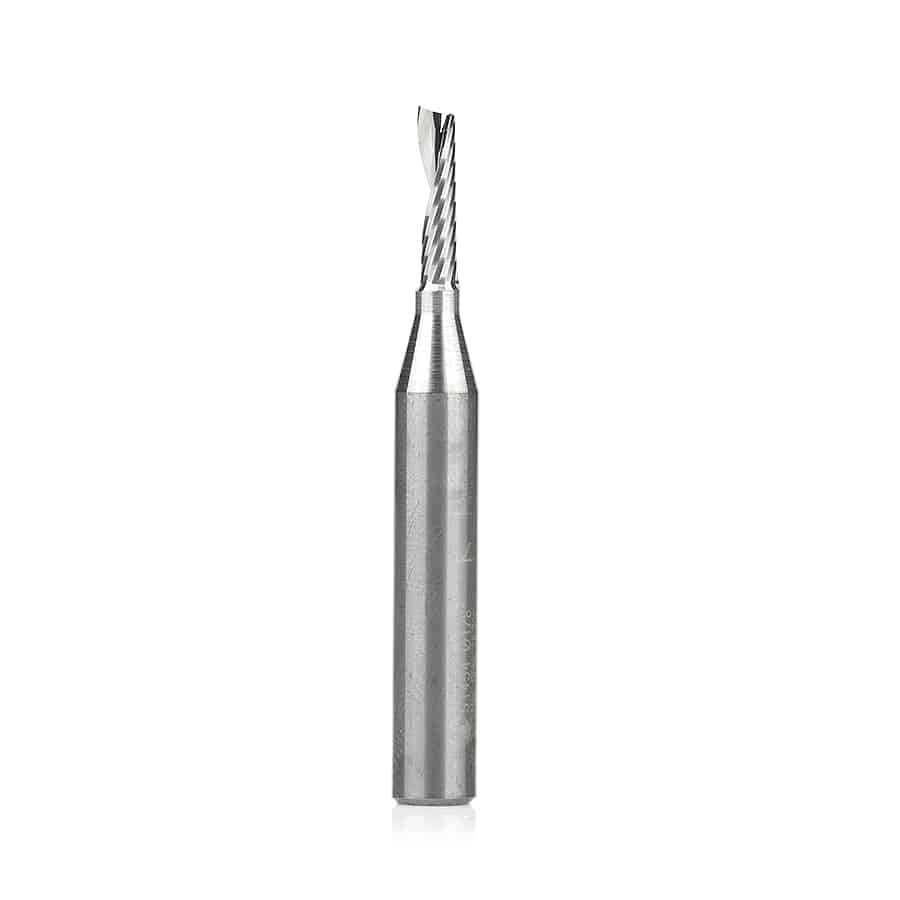
How do I know if my end mill is carbide?
Hold a magnet to it, it should have very little magnetic attraction. Also check to feel the weight of it. Carbide is extremely dense and it should feel heavy compared to its size.
How long should my carbide end mill last?
In an industrial setting tooling manufacturers sometimes quote an approximate time an endmill will last machining a specific material. The time will be for the actual cutter being ‘buried in the material’ working as hard as it can and removing a lot of steel, this ‘lifespan’ may be less than an hour.
For hobby machining though an endmill can last a long time, you will not be pushing it hard at all, the machines are just not capable of doing that.
As an example, I was machining a ‘heavy’ cut using my 3018 engraving machine with a ⅛ “ carbide end mill and the machine ground to a stop without breaking the endmill. Which tells me that the endmill is stronger than the machine.
Ball End Mills
What is a ball nose?
A ball nose end mill is just another name for a ball end mill. This type of cutter has a full radius on the end.
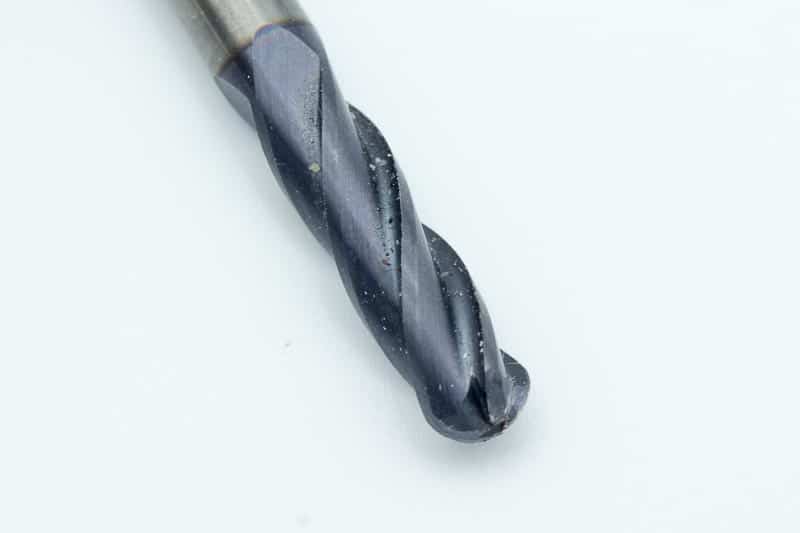
There are also bull nose end mills, these have radiused corners that are smaller than the radius of the cutter.
What is a ball end mill used for?
There are a few ball end mill uses, the big one being the ability to produce free form curves. This enables a cnc machine to machine complex flowing shapes to reproduce decorative attractive projects.
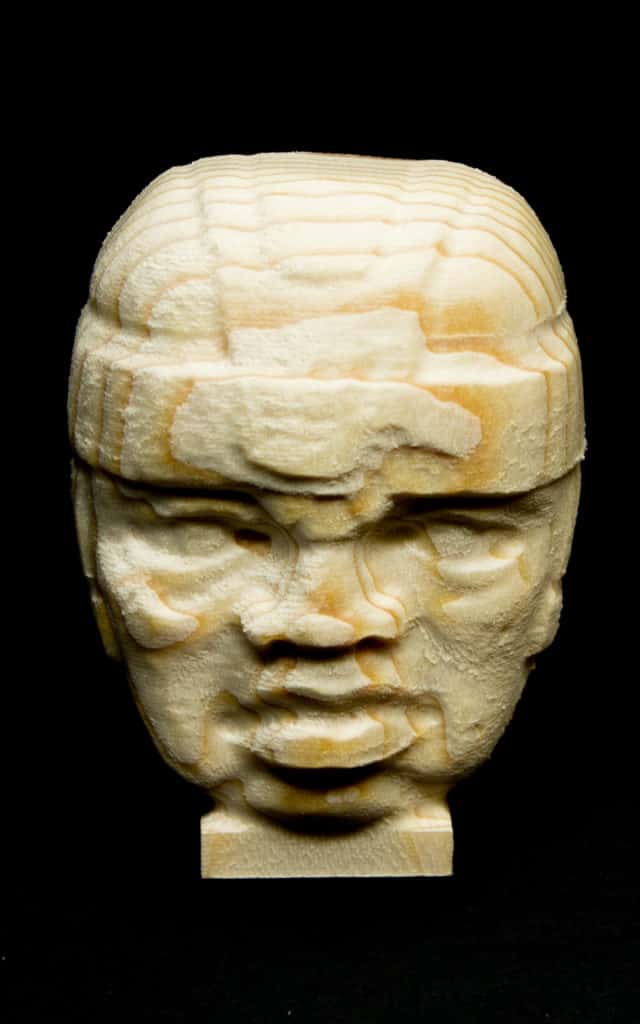
They can also create a radius in a corner:)
Tapered ball end mills
These end mills are ideal for machining reliefs and decorative projects. The radius on the end can be very small for detail work, but the taper will add a lot of strength to prevent breakage.
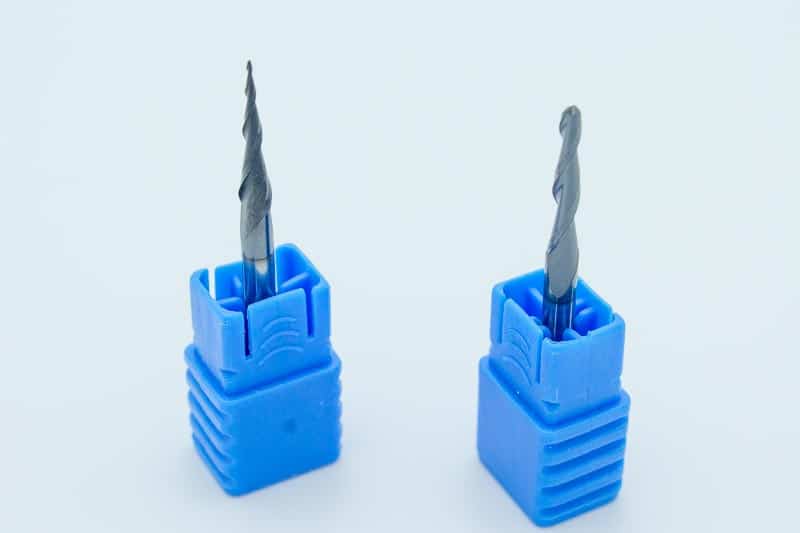
The taper will prevent you from being able to mill a vertical face but it will not be a problem on a relief, for example.
Can you plunge with a ball nose end mill?
You can, but I would try and avoid it. If you have to plunge it is a good idea to ramp down. This means moving along the X and/or Y axis while plunging at a shallow angle, i.e. less than 3 degrees.
If I was able to answer your question with this article, you can check out my site map. You will see a list of all my posts and I might be able to help you with some more cnc topics.