5-axis CNC machining is a highly advanced manufacturing technique that allows for the production of complex parts with precision and efficiency. This type of machining involves the use of computer numerical control (CNC) technology to operate a machine that can move its cutting tool in five different axes simultaneously. This enables the tool to approach the workpiece from any direction, effectively processing five sides of the part in a single setup. As a result, 5-axis machining has become an essential method for manufacturing intricate components in industries such as aerospace, automotive, and medical device production.
The key advantage of 5-axis machining, compared to its 3-axis counterpart, is the increased range of motion it provides. While 3-axis machining operates in the conventional linear X, Y, and Z axes, 5-axis machines also incorporate the rotational A and B axes. This innovative design allows for shorter cutting times, improved surface finish, and the ability to produce intricate geometries that would be either challenging or impossible with other methods.
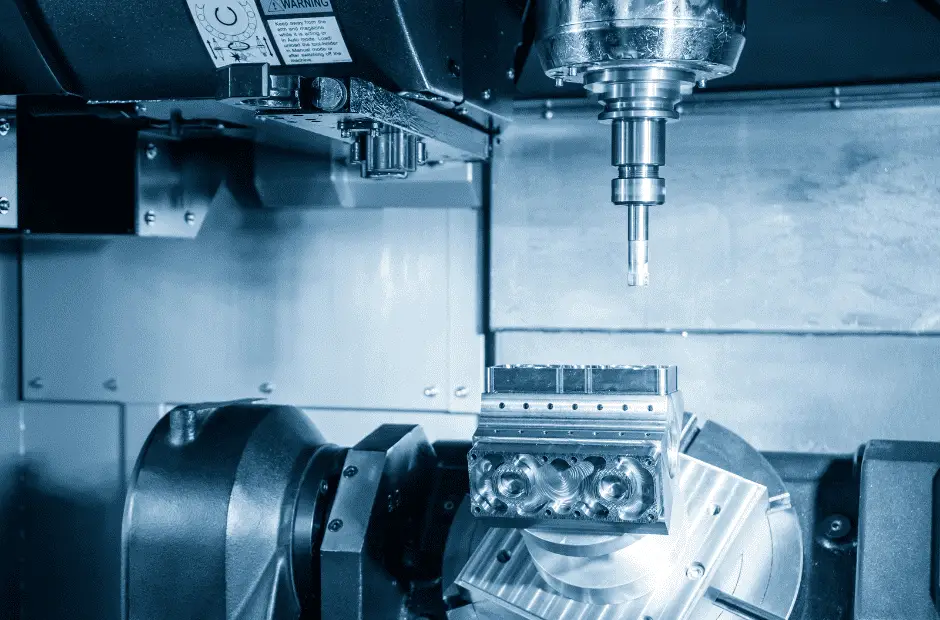
Implementing 5-axis CNC machining in a production process requires a significant investment in advanced machinery and software. However, the benefits of this technology, such as reduced setup times, enhanced precision, and the ability to produce complex components, can result in considerable cost savings and competitive advantages for manufacturers. As the demand for complex, high-quality components continues to grow, 5-axis CNC machining is expected to become even more prevalent in modern manufacturing operations.
Fundamentals of 5-Axis CNC Machining
5-Axis Machines
5-axis CNC machining is an advanced subtraction manufacturing method that utilizes a machine capable of moving its cutting tool or table in five different axes simultaneously. This technology allows for greater flexibility and precision when working on complex-shaped parts, enabling the machining of five surfaces in one single setup. This eliminates the need for multiple setups and reduces the risk of inaccuracies between each setup.
Linear and Rotational Axes
In CNC machining, there are three basic linear axes: X, Y, and Z. These represent the tool’s or table’s movement in the horizontal, vertical, and depth directions, respectively. In addition to these linear axes, 5-axis machining incorporates two rotational axes (A, B, and C) allowing the machine to rotate around these axes while maintaining precise control over its cutting movements.
A-Axis
The A-axis represents the rotation around the X-axis. This axis helps to control the angle and tilt of the cutting tool, which is especially useful when working on parts with complex or contoured surfaces that are difficult to reach with only linear movements. Having control over the A-axis helps to maintain a consistent tool/contact point on these intricate geometries, ensuring more accurate and smooth machining.
B-Axis
The B-axis represents the rotation around the Y-axis. Similar to the A-axis, having control over the B-axis allows the machine to accurately tilt and machine complex curves and surfaces. This capability significantly reduces the need for multiple setups, leading to shorter machining times and increased efficiency.
C-Axis
Finally, the C-axis represents the rotation around the Z-axis. This axis is particularly crucial when dealing with intricate parts and freeform surfaces that cannot be machined using only the X, Y, and Z linear movements. Integrating the C-axis into the 5-axis machining process enables the cutting tool to rotate 360 degrees around the part, further expanding the machine’s capabilities and improving the final product quality.
Overall, 5-axis CNC machining offers several advantages over traditional 3-axis machines, including increased efficiency, precision, and flexibility when working with complex parts. By incorporating both linear and rotational axes, 5-axis machines allow for the simultaneous machining of multiple surfaces, leading to improved accuracy and shorter lead times.
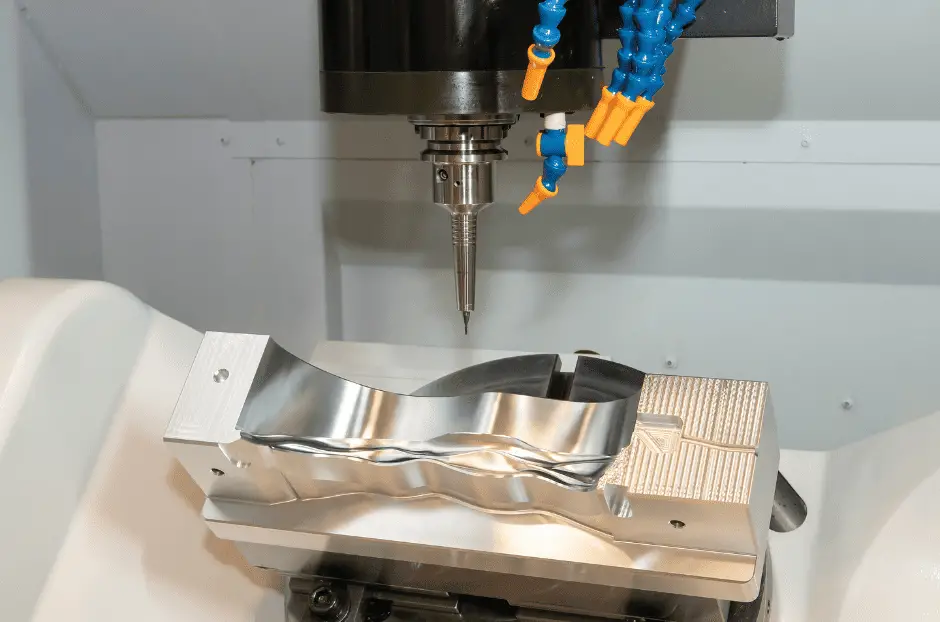
Advantages of 5-Axis CNC Machining
Improved Accuracy and Precision
One of the primary benefits of 5-axis CNC machining is the improved accuracy and precision it offers in comparison to traditional 3-axis machining. This is because 5-axis machines can access a workpiece from multiple angles, enabling it to be fully machined with fewer operations and setups. Consequently, the risk of running into the following issues is significantly reduced:
- Errors due to manual repositioning of the workpiece
- Tool deflection or vibration
- Dimensional inaccuracies
The simultaneous movement of all five axes ensures higher repeatability levels, making 5-axis CNC machine ideal for producing complex and intricate components with precision.
Reduced Setup Time and Part Handling
5-axis CNC machines reduce the need for multiple setups and manual handling of parts. Regular 3-axis machines require using separate operations, during which the workpiece must be manually repositioned to accommodate different angles. With 5-axis capability, a single setup can accommodate multiple faces and orientations of the workpiece, thus streamlining the production process.
Reduced setup time and part handling increase the following:
- Production speed
- Efficiency
- Consistency
Increased Surface Quality and Finishing
Utilizing a 5-axis CNC machine often results in superior surface quality and finishes. Because the machine head can approach the part from various angles, it allows for the use of shorter cutting tools while maintaining surface contact. Shorter tools are less prone to vibration, which ultimately leads to better surface finishes. Utilizing advanced Cam machining techniques, such as Trochoidal Milling further improves tool life and efficiency.
By using a 5-axis CNC machine, it is possible to achieve:
- Tighter tolerances
- Increased cutting speeds
- Reduced material waste
Labor and Production Efficiency
The advanced capabilities of 5-axis CNC machines not only enhance productivity but also optimize labor efficiency. The need for highly skilled operators and manual intervention is considerably reduced, as these machines can complete multi-faceted tasks during a single operation. This, in turn, allows workers to focus on quality control, inspecting multiple parts simultaneously, and managing other tasks outside of machining operations.
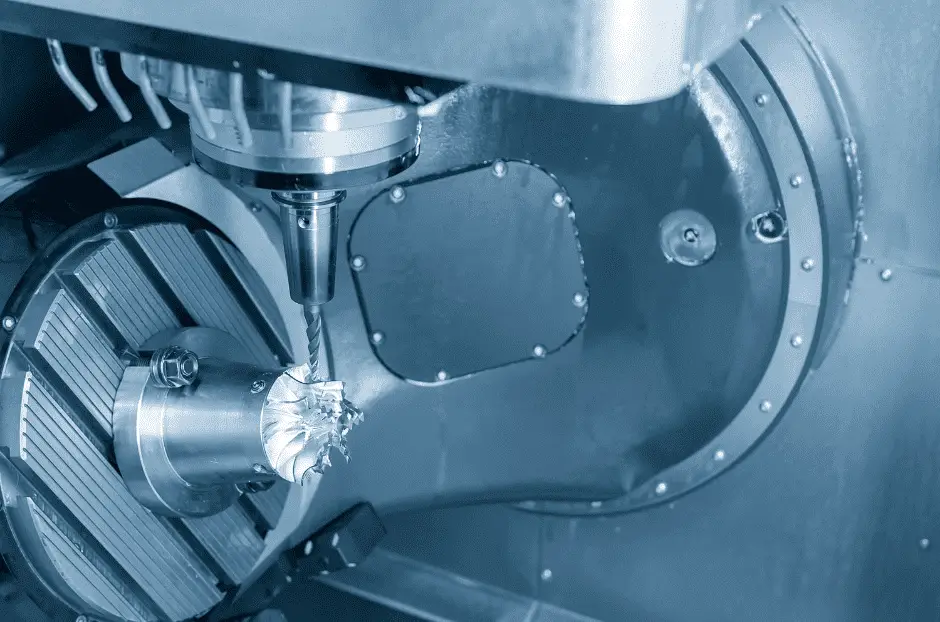
5-Axis CNC Machining Process
Programming
The programming aspect of 5-axis CNC machining is essential for achieving precision and optimal efficiency. This process requires the use of CAD/CAM software to design and generate toolpaths. The software converts the 3D models into a series of instructions, known as G-code, which guides the cutting tool’s movement along the five axes. Successful programming not only improves cutting performance but also reduces the risk of errors during machining.
Tool and Workpiece Setup
Proper setup of the cutting tool and workpiece is crucial for effective 5-axis CNC machining. The workpiece is usually clamped onto the CNC machine’s table, which can move along the X, Y, and Z axes. Additionally, two rotary axes (A, B, and C) are responsible for the rotation of either the workpiece or the cutting tool, providing even more possibilities for machining complex geometries. Attention to the setup process ensures that the workpiece remains stable and aligned during the cutting phase, thus improving the final product’s quality.
Cutting and Material Removal
The 5-axis CNC machining process involves the simultaneous movement of the cutting tool along multiple axes. This allows for intricate cuts and the ability to work with a wide variety of materials, such as metal, plastic, and wood. The speed, depth, and direction of the cutting process are determined by the G-code generated during programming.
Different cutting tools are used based on the desired end result and the material being machined. These tools must be carefully chosen and maintained to ensure optimal cutting performance and extend their lifespan. Some key factors to consider when selecting a cutting tool are:
- Material compatibility
- Tool geometry
- Cutting speed and feed rate
Using the right cutting tool not only enhances cutting performance but also reduces the amount of waste generated during the machining process. Additionally, proper use and maintenance of these tools can contribute to increased efficiency and cost savings for the operator.
Types of 5-Axis CNC Machining
Simultaneous 5-Axis Machining
Simultaneous 5-axis machining, as the name suggests, involves the coordinated movement of all five axes during the machining process. This allows the cutting tool to maintain a continuous relationship with the workpiece, providing smooth and precise results. In simultaneous 5-axis machining, the cutting tool can move freely in the X, Y, Z, A, and B axes, which enables it to carve complex geometries and contours that would be impossible or extremely difficult with traditional 3-axis machining. This process is particularly well-suited to making parts for industries such as aerospace, automotive, and mold manufacturing, where high precision and complexity are required.
Some of the benefits of simultaneous 5-axis machining include:
- Reduced setup time, as complex parts can be machined in a single setup
- Improved surface finish, as the tool maintains a consistent angle relative to the workpiece throughout the process
- Greater flexibility in the types of geometries that can be machined
Continuous 5-Axis CNC Machining
Continuous 5-axis CNC machining is another type of 5-axis machining in which the cutting tool and workpiece maintain their relationship throughout the machining process. The difference between continuous and simultaneous 5-axis machining lies in the order of operations – in continuous 5-axis machining, the tool completes one cut at a time along the X, Y, Z, A, and B axes, then moves to the next. This approach can be more efficient for certain applications, as the tool spends less time repositioning between cuts.
Continuous 5-axis machining offers several advantages, such as:
- Increased accuracy, as the tool moves along a continuous path, reducing the risk of errors caused by tool repositioning
- Improved flexibility in machining complex geometries and contours
- Potential for increased tool life, as the consistent tool orientation can help reduce wear on the cutter
While both simultaneous and continuous 5-axis CNC machining provide increased capabilities compared to traditional 3-axis machining, they each have their own unique advantages and applications. Selecting the appropriate method depends on factors such as the complexity of the part, the desired level of accuracy, and the specific industry requirements.
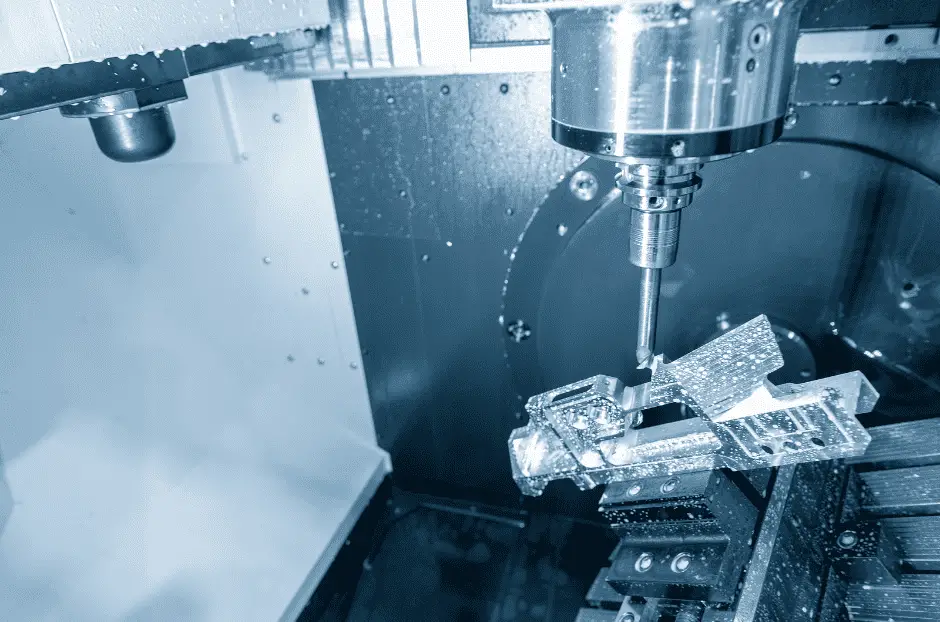
5-Axis CNC Machine Tools and Components
CNC Controllers and Systems
CNC systems and controllers play a vital role in 5-axis machining by managing the multi-axis movements and advanced functions needed for optimal tool paths. Some popular CNC systems for 5-axis machines come from manufacturers like FANUC. These systems are known for their reliability and compatibility with CAD/CAM software used in different industries.
Rotary Table and Trunnion
The rotary table and trunnion are crucial components in 5-axis machining centers. The rotary table allows for the precise rotation of the workpiece, while the trunnion holds the workpiece in place and ensures stability during the machining process. These components work together to enable accurate and efficient 5-axis machining operations.
Vertical and Horizontal 5-Axis Machines
5-axis CNC machines can be categorized into two main types: vertical and horizontal. Vertical 5-axis machines typically have a spindle that moves in the X, Y, and Z axes, while the workpiece rotates around the A and B axes. In contrast, horizontal 5-axis machines have a spindle that moves in the X, Y, and Z axes, and the workpiece rotates around the B and C axes. Both types of machines offer advantages and are chosen based on the technical requirements and specific needs of the given project.
Tool Center Point
The Tool Center Point (TCP) is an essential aspect of 5-axis machining. TCP is the point at which the cutting tool makes contact with the workpiece, and maintaining control over this point is crucial for accurate and efficient machining operations. Advanced CNC systems, such as Dynamic Work Offsets/Tool Center Point Control (DWO/TCPC), enable operators to create CAM programs ahead of time, allowing for the placement of the work holding and part anywhere on the table without having to repost the program.
5-axis CNC machines and their components have become integral tools in modern manufacturing processes. With the advancements in CNC controllers and systems, rotary tables, trunnions, and the combination of vertical and horizontal machines, 5-axis machining centers enable a higher level of precision and efficiency, catering to a wide range of industries and applications.
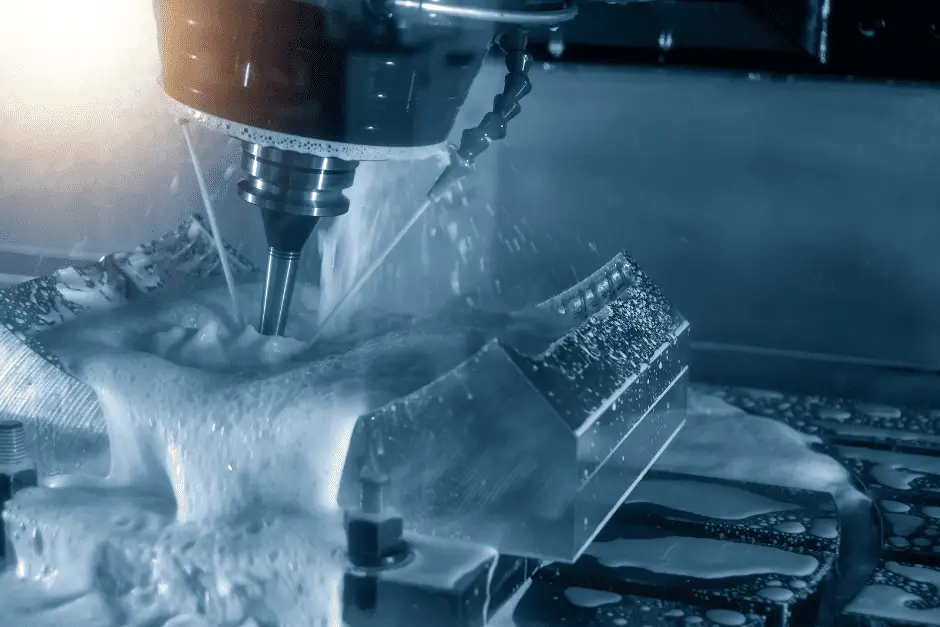
Industries and Applications
5-axis CNC machining has become increasingly popular and essential across various industries, primarily due to its ability to create complex geometries and manufacture intricate parts with high precision. In this section, we will explore the applications and benefits of 5-axis CNC machines in the aerospace, automotive, and medical industries.
Aerospace Industry
The aerospace industry demands extremely high precision and quality when manufacturing its components. 5-axis CNC machines are perfect for this industry, as they can produce complex geometries and intricate parts with tight tolerances required for aerospace applications. Some common uses for 5-axis CNC machining in the aerospace industry include:
- Manufacturing aircraft engine components
- Producing airframe and fuselage parts
- Creating landing gear components
- Fabricating satellite components and housings
Utilizing 5-axis machine tools in the aerospace industry allows for reduced setup times, enhanced surface quality, and improved overall production efficiency.
Automotive Industry
Similarly, the automotive industry greatly benefits from the use of 5-axis CNC machines. As automotive components become increasingly complex and require tighter tolerances, these machines offer a solution. Applications for 5-axis CNC machining in the automotive industry include:
- Engine components, such as cylinder heads and engine blocks
- Complex gearbox components, including gears and housings
- Suspension and brake system components
- Molds and dies for body panels
By using 5-axis CNC machines in automotive manufacturing, companies can ensure that their parts meet strict quality standards and improve production efficiency.
Medical Industry
The medical industry also relies on 5-axis CNC machines for manufacturing intricate and complex parts. These components demand high precision and tight tolerances in order to function properly and ensure patient safety. Some common applications of 5-axis CNC machining in the medical industry include:
- Orthopedic implants, such as knee and hip replacements
- Surgical instruments, including endoscopic and laparoscopic tools
- Dental prosthetics, like crowns and bridges
- Components for diagnostic and imaging equipment
Incorporating 5-axis CNC machines into medical device manufacturing helps maintain the highest levels of accuracy and repeatability, ultimately providing safe and effective medical products for patients.
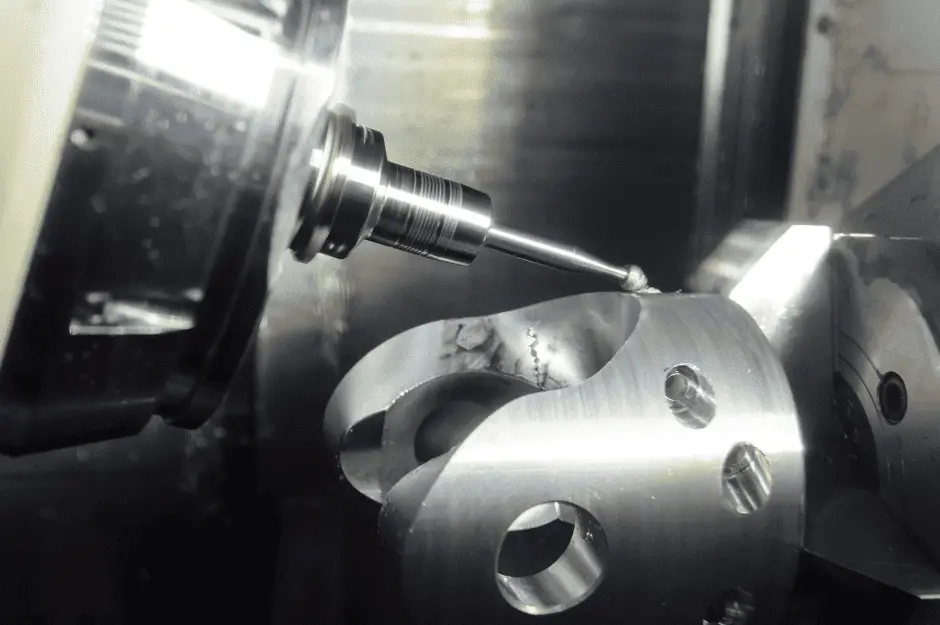
Challenges and Solutions in 5-Axis CNC Machining
5-axis CNC machining offers numerous advantages in terms of precision and flexibility, but it also comes with its fair share of challenges. Understanding these challenges and identifying effective solutions is crucial for maximizing the benefits of this advanced machining technique.
Tool Accessibility and Reach
One of the primary challenges in 5-axis CNC machining is ensuring optimal tool accessibility and reach to all areas of the workpiece. The complex geometry and intricate features of certain parts can make it difficult for the cutting tool to reach specific areas without collision or interference. This challenge often arises when machining deep pockets, undercuts, or narrow channels.
To overcome this challenge, engineers and programmers must carefully plan the toolpath to avoid collisions and ensure proper clearance. Advanced CAM software with collision detection capabilities can help simulate and optimize toolpaths, identifying potential collision points and offering alternative approaches. Additionally, using shorter and more specialized cutting tools, such as tapered end mills or extended reach tools, can enhance tool accessibility and mitigate interference issues.
Machining Accuracy and Part Quality
Achieving high machining accuracy and superior part quality in 5-axis CNC machining can be demanding due to factors like tool deflection, machine dynamics, and workpiece fixturing. As the cutting tool moves along complex toolpaths and angles, it generates varying cutting forces that can result in tool deflection and, consequently, diminished accuracy.
To address this challenge, it is essential to utilize robust and rigid machining setups to minimize machine vibrations and ensure stability. Properly aligning and securing the workpiece on the machine table using accurate and reliable fixturing techniques is crucial for maintaining dimensional precision. Additionally, employing high-performance cutting tools made from advanced materials with improved rigidity and reduced deflection can enhance machining accuracy and overall part quality.
Programming Complexity
Compared to traditional 3-axis CNC machining, programming for 5-axis CNC machines can be more intricate and time-consuming. The added axes introduce additional degrees of freedom and complexity in defining tool orientations and creating toolpaths. Moreover, the coordination of simultaneous and synchronized movements of multiple axes requires meticulous programming expertise.
To simplify programming for 5-axis CNC machining, utilizing advanced CAD/CAM software that offers intuitive user interfaces and powerful toolpath generation capabilities can significantly streamline the process. These software tools often include automated features for toolpath optimization, collision detection, and adaptive machining strategies, reducing the programming complexity and enhancing overall efficiency.
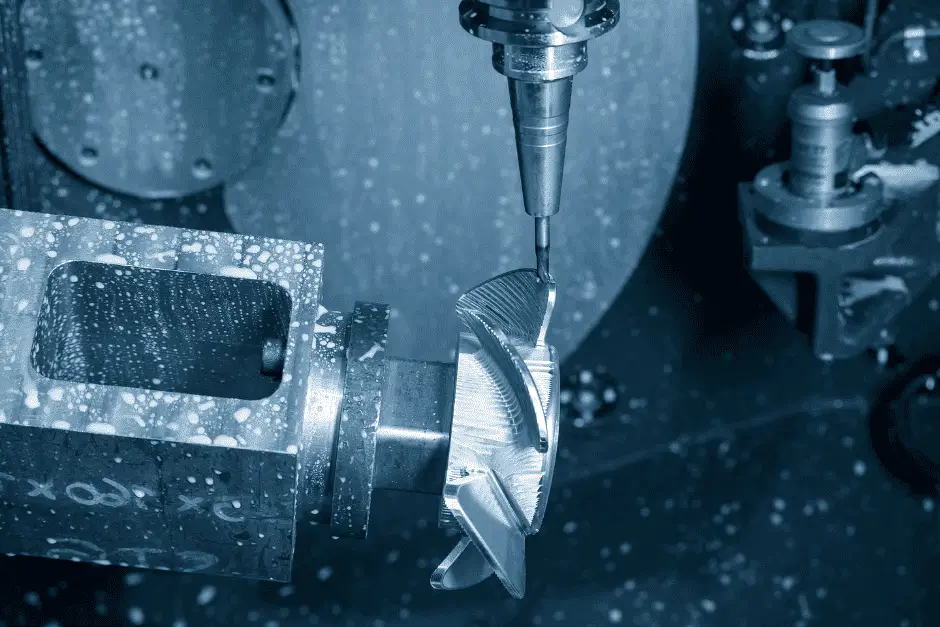
Cost and Investment
Implementing 5-axis CNC machining in a manufacturing facility involves specific costs and investments. While the initial expenses might be higher compared to traditional machining methods, the benefits and potential returns often outweigh the investment in the long run.
The cost considerations associated with 5-axis CNC machining can be broadly categorized into equipment, tooling, programming, and training.
Equipment Costs
Investing in a 5-axis CNC machine entails a significant upfront cost. The complexity and advanced capabilities of these machines make them more expensive than their 3-axis counterparts. Factors such as machine size, spindle power, automation features, and overall build quality influence the price range. Additionally, the cost of necessary peripherals and accessories like workholding fixtures, tool holders, and cutting tools should be taken into account.
Tooling Costs
Tooling costs for 5-axis CNC machining may vary depending on the complexity of the parts being produced, the desired surface finish, and the material being machined. The need for specialized cutting tools, such as long-reach or tapered end mills, can contribute to the overall tooling expenses. It is crucial to consider tool life, tool quality, and the potential for regrinding or reconditioning to optimize tooling costs.
Programming Costs
The programming aspect of 5-axis CNC machining also incurs costs. This includes the expenses associated with acquiring and maintaining CAD/CAM software packages capable of generating complex toolpaths and optimizing machining strategies for 5-axis operations. The cost of software licenses and updates should be factored into the overall investment.
Training Costs
To fully leverage the benefits of 5-axis CNC machining, operators and programmers need adequate training to understand the intricacies of the technology and optimize its usage. Training programs, either provided by the machine manufacturer or through external resources, can incur additional costs. However, investing in comprehensive training ensures that the operators have the necessary skills to program, set up, and operate the 5-axis CNC machine efficiently, minimizing errors and maximizing productivity.
Although the initial investment in 5-axis CNC machining may be higher compared to traditional machining methods, the technology offers various advantages that can lead to long-term cost savings. These advantages include increased productivity, reduced setup time, improved part quality, and enhanced machining efficiency. Evaluating the potential return on investment (ROI) by considering factors such as increased throughput, reduced scrap rates, and improved overall process optimization is crucial when assessing the cost implications of implementing 5-axis CNC machining.
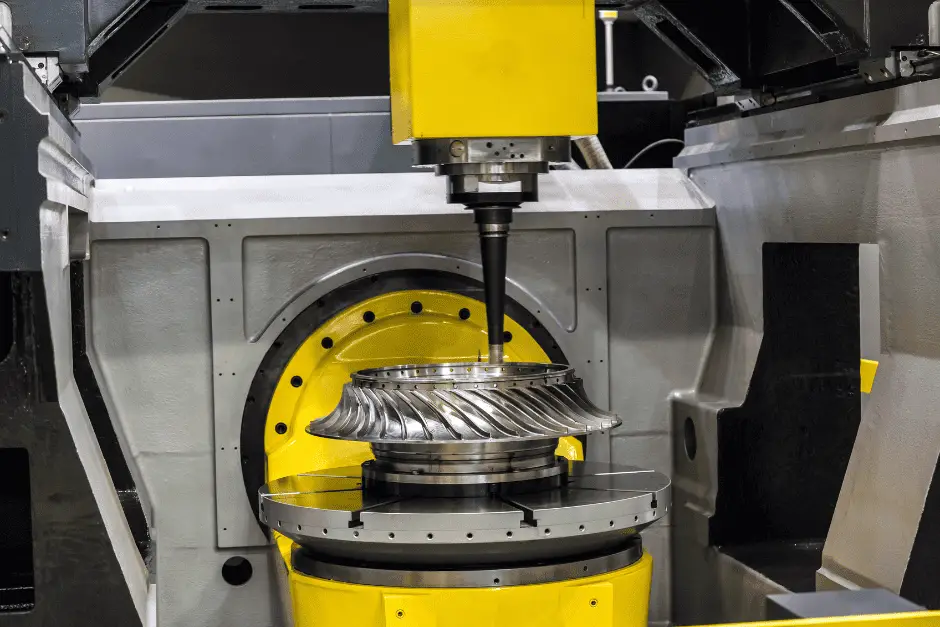
Programming and Training
The successful implementation of 5-axis CNC machining heavily relies on effective programming and comprehensive training. The complexity of programming for 5-axis machines and the need for skilled operators necessitate careful consideration of these aspects.
Programming for 5-Axis CNC Machining
Programming for 5-axis CNC machining involves creating toolpaths that accurately define the tool’s position and orientation as it moves along multiple axes simultaneously. This process requires advanced CAD/CAM software that provides intuitive interfaces and powerful toolpath generation capabilities.
To program for 5-axis CNC machining, operators must consider factors such as tool accessibility, collision avoidance, and optimized toolpaths. Utilizing advanced CAM software with collision detection and simulation features allows operators to visualize potential collisions and make necessary adjustments to ensure safe and efficient machining.
Moreover, programming for 5-axis machining often involves strategies like continuous 5-axis machining, 3+2 axis machining, or simultaneous 5-axis machining, depending on the complexity of the part and its design requirements. Operators must have a deep understanding of these strategies and be proficient in utilizing the software tools to generate efficient and accurate toolpaths.
Training for 5-Axis CNC Machining
Training plays a vital role in unlocking the full potential of 5-axis CNC machining. Skilled operators and programmers are essential for maximizing productivity and ensuring optimal utilization of the technology.
Training programs for 5-axis CNC machining cover a range of topics, including machine operation, toolpath generation, fixture design, machine maintenance, and troubleshooting. These programs can be provided by machine manufacturers, training institutes, or industry experts.
Hands-on training with the specific 5-axis CNC machine that will be used in production is crucial. Operators learn how to set up workpieces, fixture them securely, load tooling, and optimize machining parameters. Additionally, training should cover programming techniques, including understanding toolpath strategies, using CAD/CAM software effectively, and troubleshooting common programming issues.
Regular training updates and refresher courses are recommended to keep operators and programmers up to date with the latest advancements in 5-axis CNC machining technology and programming techniques. This ongoing investment in training ensures that the team maintains a high level of competence and efficiency in utilizing 5-axis CNC machines.
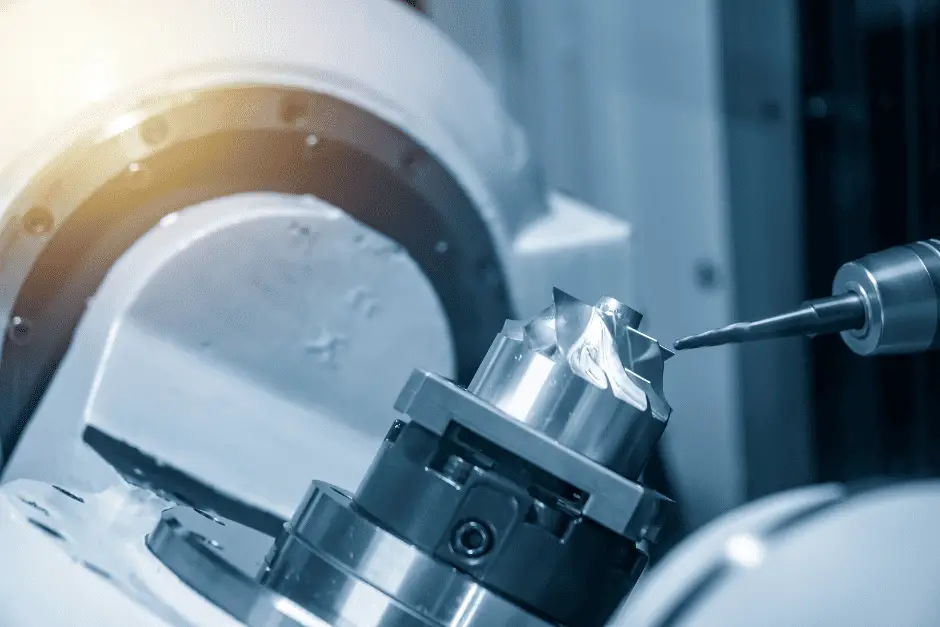
Automation and Integration
Automation and integration play significant roles in enhancing the productivity and efficiency of 5-axis CNC machining operations. By automating certain processes and integrating the 5-axis CNC machine into the overall manufacturing workflow, manufacturers can optimize throughput, reduce cycle times, and improve overall process control.
Tool and Workpiece Management
Automation can be implemented in tool and workpiece management to streamline the 5-axis CNC machining process. Automatic tool changers and tool presetting systems enable the machine to change tools seamlessly without manual intervention, reducing setup time and increasing productivity. These systems can also track tool life and automatically initiate tool replacement when necessary, minimizing downtime and optimizing tool utilization.
Similarly, workpiece management can be automated by incorporating robotic systems for workpiece loading and unloading. By integrating robots with the 5-axis CNC machine, manufacturers can achieve continuous production with minimal operator intervention. This not only reduces labor costs but also ensures consistent and efficient handling of workpieces, improving overall process efficiency.
Data Integration and Process Monitoring
Integrating the 5-axis CNC machine with the manufacturing execution system (MES) or enterprise resource planning (ERP) system enables real-time data exchange and process monitoring. This integration facilitates seamless communication between different stages of the manufacturing workflow, such as design, programming, machining, and quality control.
Real-time data monitoring allows operators and managers to track machine performance, identify potential issues, and make data-driven decisions for process optimization. It enables predictive maintenance by monitoring machine health and performance parameters, thereby minimizing unplanned downtime and maximizing machine availability.
Advanced Machining Technologies
Automation and integration also enable the implementation of advanced machining technologies in 5-axis CNC machining. For example, the use of probing systems integrated with the machine allows for in-process part measurement and feedback. This enables automatic tool offset adjustments, compensating for any variations in workpiece dimensions or tool wear. The result is improved machining accuracy and reduced scrap rates.
Additionally, incorporating adaptive machining strategies, such as toolpath optimization based on real-time cutting conditions or intelligent feedrate control, can further enhance the efficiency and performance of 5-axis CNC machining. These advanced technologies leverage automation and integration to optimize cutting parameters dynamically, ensuring optimal tool engagement and minimizing machining time.
By embracing automation and integration in 5-axis CNC machining, manufacturers can unlock the full potential of this advanced technology. It streamlines the manufacturing process, improves productivity, enhances quality control, and enables the implementation of advanced machining techniques for better efficiency and competitiveness.